Home » Palletizer
Palletizer
Senieer intelligent palletizer is efficient, safe and accurate, and can easily handle a variety of material stacking needs, optimize the production process, reduce labor costs and accidents, and make your production line more competitive.
Introduction of Palletizer
A palletizer is an industrial device used to automatically stack goods, boxes, bags or other items neatly on pallets or designated areas for transportation or storage. Through efficient automation technology, palletizers can significantly reduce manual labor, improve stacking speed and accuracy, ensure stacking stability and safety, and maximize the warehouse space used. They are suitable for a variety of industries such as logistics, manufacturing, and food processing.
It optimizes overall production management with their efficient and precise automated operations. In order to meet different scenarios and production needs, Senieer provides a variety of palletizer models, each with unique design and functional advantages.
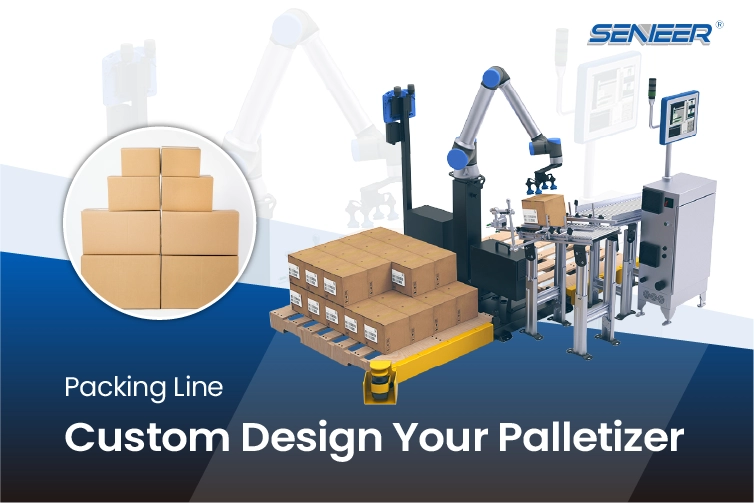
Different Types of Palletizers
Palletizers can usually automatically grab materials(boxes, bags, or crates) and stack them on pallets or designated locations in an orderly manner according to a preset program. A wide range of equipment types, including robotic palletizers, gantry palletizers, hybrid palletizers, and High-Level palletizers can be configured to suit specific needs. Senieer offers automatic or semi-automatic palletizers to meet various production needs of clients. By reducing human involvement, palletizers offer huge advantages in increasing efficiency and reducing human error and safety accidents.
Find Palletizers according to your industry or process
Palletizers play a vital role in many industries. Their flexibility and efficiency enable logistics, food processing, pharmaceuticals, chemicals and other fields to significantly improve production efficiency and stacking quality. Whether handling heavy industrial materials or precisely stacking fragile products, palletizers provide customized solutions for different industries. Through orderly stacking and store, the shipping of large quantities of goods with the least number of packages is possible. Next, we will delve into the specific applications of palletizers in various industries and the value enhancement they bring.
The advanced technology of palletizer is the core to achieve efficient automated stacking, covering every aspect from material grabbing and positioning to precise stacking. This automated process not only improves the production speed, but also ensures the stability and safety of stacking, adapting to the needs of various production environments. Its working process briefly includes:material feeding by conveyor belt, orientation and grouping, layer formation, pallet stacking, etc.
Guidelines For Palletizer
This guide provides detailed information including equipment installation, operating procedures, safety precautions and maintenance tips to ensure you get the most out of this machine.
Characteristics of Palletizer
The design and functional characteristics of a palletizer determine its suitability for different industries. Modern palletizers have the characteristics of intelligent control, precise and efficient operation, making them an indispensable automation equipment in the production line.
1.High-precision operation: Using advanced sensors and control systems, the palletizer can accurately grab and place materials to ensure stacking stability and neatness.
2.Versatility: Supports processing of a variety of material forms, such as boxes, bags, barrels, etc., and can adapt to products of different sizes and weights.
3.Modular design: easy to expand and maintain, users can adjust equipment configuration according to specific production needs, reducing the cost of equipment replacement and upgrades.
4.Intelligent control: equipped with an advanced automated control system with adaptive learning function, which can optimize the operating process and improve production efficiency.
Advantages of Palletizer
Choosing a palletizer can not only improve stacking efficiency, but also reduce labor costs, improve production safety, and bring many substantial benefits. Compared with traditional manual stacking, the advantages of intelligence and automation of palletizers are obvious.
1.Improve efficiency: Automated stacking significantly speeds up the production pace and reduces the time for stacking goods, especially in high-volume production lines.
2.Reduce labor costs: Reducing reliance on manual operations not only saves labor costs, but also reduces the risk of employee fatigue and operational errors. By palletizer solutions, the personnel expenses of our clients has been reduced by 60%.
3.Optimize space utilization: Through precise stacking, palletizers help companies maximize the use of storage space and improve the efficiency and safety of material storage.
4.Enhanced safety: Reduces the need for workers to participate in the handling and stacking process, reducing the risk of workplace injuries caused by heavy lifting or operating errors. According to statistics from clients, the accidents rate in their factories and labs has been reduced by 50%.
How Does Palletizer Work?
The automated operation of the palletizer relies on a highly precise working principle. This system supports every link from material handling to stacking, making the production process smoother and more efficient. The following is the working processes of palletizers.
- Material identification and positioning
The work of the palletizer begins with the identification and positioning of the materials to be processed. Sensors and cameras are installed on the equipment to monitor materials on the conveyor belt in real time. These sensors can detect the location, shape, size and weight of materials, ensuring that the equipment can choose the best gripping method.
- Crawl system
After identifying the material, the palletizer’s grabbing system will start. Most palletizers use gripping tools (such as vacuum cups, clamps) equipped with robotic arms to grasp materials. The gripper system is designed so that it can handle products of many shapes and sizes to meet different stacking needs.
- Vacuum suction cup: suitable for flat materials, such as cartons or plastic bags, to absorb the materials through negative pressure.
- Clamp: Suitable for items with irregular shapes or heavy weight, providing stronger gripping force.
- Moving and stacking
After grabbing the material, the robotic arm will move the material to the designated stacking location according to the set program. At this time, the movement system of palletizer (such as servo motor or pneumatic device) will accurately control the movement trajectory and speed of the robotic arm to ensure the safety and accurate stacking of materials.
- Stacking mode
The palletizer can choose different stacking modes according to needs, such as staggered stacking, straight stacking or square stacking, etc. These modes can optimize the stacking structure and improve space utilization and transportation safety based on the characteristics of the materials and transportation requirements.
- Automatic pallet change
When a pallet is full, the palletizer automatically replaces a new pallet and continues the next stacking process. This process is usually completed by a pallet changing device to ensure the continuity of the production line without interrupting operations due to pallet replacement.
- System control and monitoring
The entire process is managed by a central control system, which can set different working modes through programming, monitor the operating status of the equipment, and conduct timely fault diagnosis and alarms. Modern palletizers are often equipped with a human machine interface (HMI) to facilitate operator setup and monitoring.
Applications
1.Pharmaceutical industry
The pharmaceutical industry has extremely high requirements for material safety and handling accuracy.
①Pharmaceutical packaging: Before pharmaceuticals leave the factory, the palletizer can efficiently stack pharmaceutical packaging boxes neatly and reduce the risks caused by human operations.
②Compliant stacking: Ensure industry standards are met during stacking to avoid contamination and confusion.
2. Logistics and warehousing
In the logistics and warehousing industry, palletizers are widely used for automated stacking and storage of goods. By efficiently handling different types of packaging (such as cartons, boxes, plastic bags, etc.), palletizers can greatly improve the efficiency of goods access. Specific applications include:
①Pallet stacking: Quickly stack goods onto pallets, ready for shipping or storage.
②Automatic sorting: Combined with the automated sorting system, the palletizing machine can automatically classify and stack goods according to order requirements.
3. Food and Beverages
The food and beverage industry has strict requirements for product safety and hygiene, and palletizers help companies in these industries achieve efficient stacking and packaging from cans and bottles to bags of flour or sugar. Application scenarios include:
①Bottled beverages: Automatically stack bottled water, beverages and other products neatly to ensure stability during transportation.
②Food packaging: Handle various food packaging (such as cartons, plastic trays, bags, etc.) to ensure product safety and compliance with hygienic standards.
4. Chemical industry
Chemical products often present certain hazards, and palletizers in the chemical industry help handle these materials safely and efficiently. Application scenarios include:
①Heavy-duty bagged chemical raw materials: The palletizer can handle large bags of chemical fertilizers, plastic granules and other heavy materials to improve stacking efficiency.
②Safe stacking: Ensure the safety of chemical products during transportation and storage to avoid leaks and accidents caused by improper stacking.
If you are interested in this automated machine, please feel free to contact us.
Choose Your Interested Production Line
Bottle Filling Line
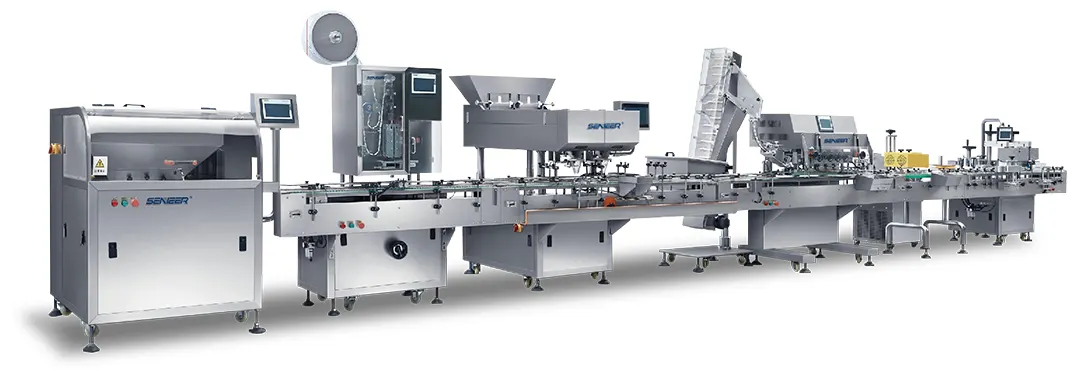
Granulation Line
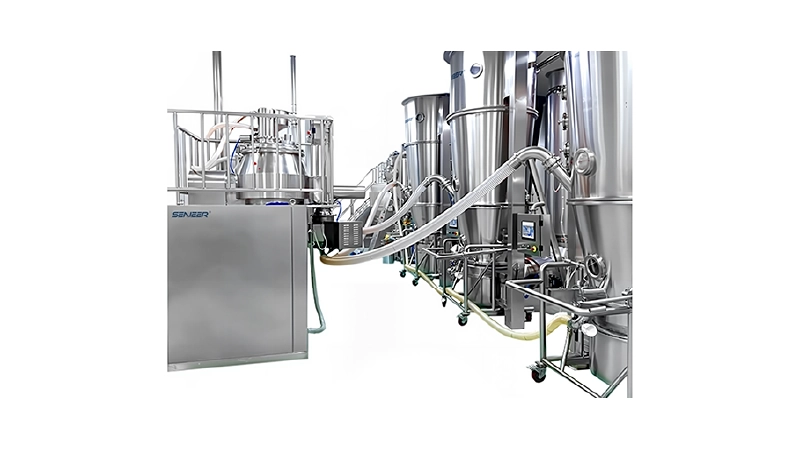
Blister Packaging Line
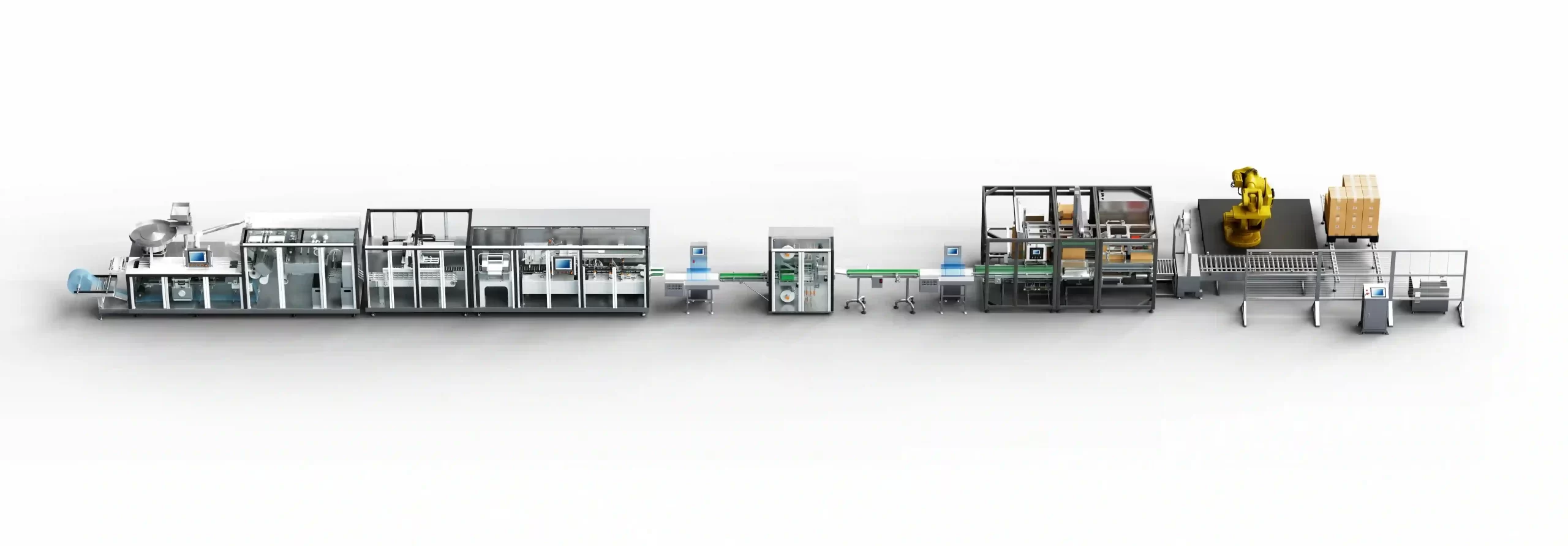
Powder Filling Line
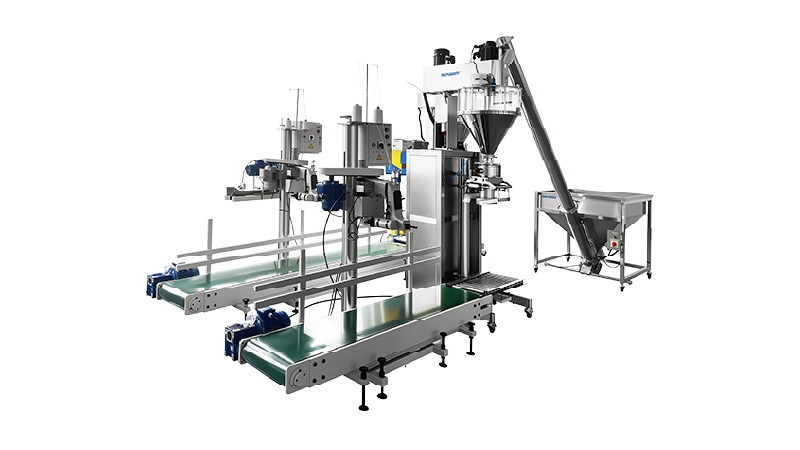