Cone Valve IBC
Solve the common problems of material segregation, bridging, rat-holing, blocking and others that occur in the traditional butterfly or other valves. Senieer Cone Valve IBC offers automatic, dust-free and enclosed filling and discharging of materials.
Introduction of Cone Valve IBC
Cone Valve IBC (the Intermediate bulk containers with cone valve) is a portable hopper that is used to transfer, store or mix multiple materials such as powder, granules, pellets or flakes. It is widely used in new energy lithium batteries, food, medicine and chemical industries. Senieer IBC system adopts unique cone valve technology to solve the commonly happened problems of traditional butterfly and star valves, such as the rat holing, material segregation, bridging, material residuals, blocking, etc. Cone Valve IBC includes or can be quipped with the following four parts: fixed station for cone valve, vibratory discharge cone valve,automated lid-lifting device, post bin blender.
The cone valve can be set to automatically vibrate to control the material flowing in the IBC hoppers. Cone Valve IBC can achieve the dust-free, hygienic, residual-free and efficient discharge of materials.
Different Types Of Cone Valve IBCs
According to the different classification standards, there are diverse Cone Valve IBCs. Classified according to the body materials used, Cone Valve IBC has the following types: the standard(stainless steel)Cone Valve IBC range(mainly for food and pharmaceutical fields), the polyethylene Cone Valve IBC range(for non-food application), the mild steel Cone Valve IBC range. Classified as per the capacity, there are 500L, 750L, 1250L, 1500L Cone Valve IBCs. Senieer also offers customization service. According to the requirements of clients, Senieer can design Cone Valve IBCs with specific material and capacity.
Find Cone Valve IBC According To Your Industry Or Process
Cone Valve IBC is widely used in many fields like pharmaceutical, food, medicine, chemical and new energy lithium batteries due to its automatic, efficient, dust-free, hygienic and safe feeding, blending, and discharging of materials. As a decoupled system, Senieer Cone Valve IBC can be used simultaneously between different production processes to increase the production efficiency and reduce downtime due to its portable properties. For example, one serves as a feeding container, the second one is used to blend materials, the third one is discharging materials while the fourth one is being cleaned for usage. This decoupled system enables you to produce products at any time without the downtime.
Cone Valve IBC system mainly include the following four parts: fixed station for cone valve, vibratory discharge cone valve,automated lid-lifting device, post bin blender. The fixed station for cone valve is used for material receiving station. Automated lid-lifting device is used for lid-lifting station, fully automation and no need for manual intervention. Discharging station, used for discharging materials, is used in conjunction with Senieer cone valve IBC, which has a function of vibratory discharging, the discharge volume can be controlled. Vibratory discharge cone valve, it is a conical structure with an automatic vibratory function.
Guidelines For Cone Valve IBC
As an industrial bulk container, Cone Valve IBC is mainly applied in the powder/bulk handling system, as a part of storage, transfer, blending and discharging production processes. Compared to traditional bulk bag, Senieer Cone Valve IBC overcomes many disadvantages which is usually unavoidable in the bulk bag system. By adopting specially developed cone valve technology, achieving fully automatic discharge of material, reducing manual interference and avoiding problems of bridging, blocking, and material segregation. According to the needs of clients, there are two modes of discharging: continuous and intermittent.
Key Configuration And Characteristics Of Cone Valve IBC
The system of Cone Valve IBC consists of the following parts:
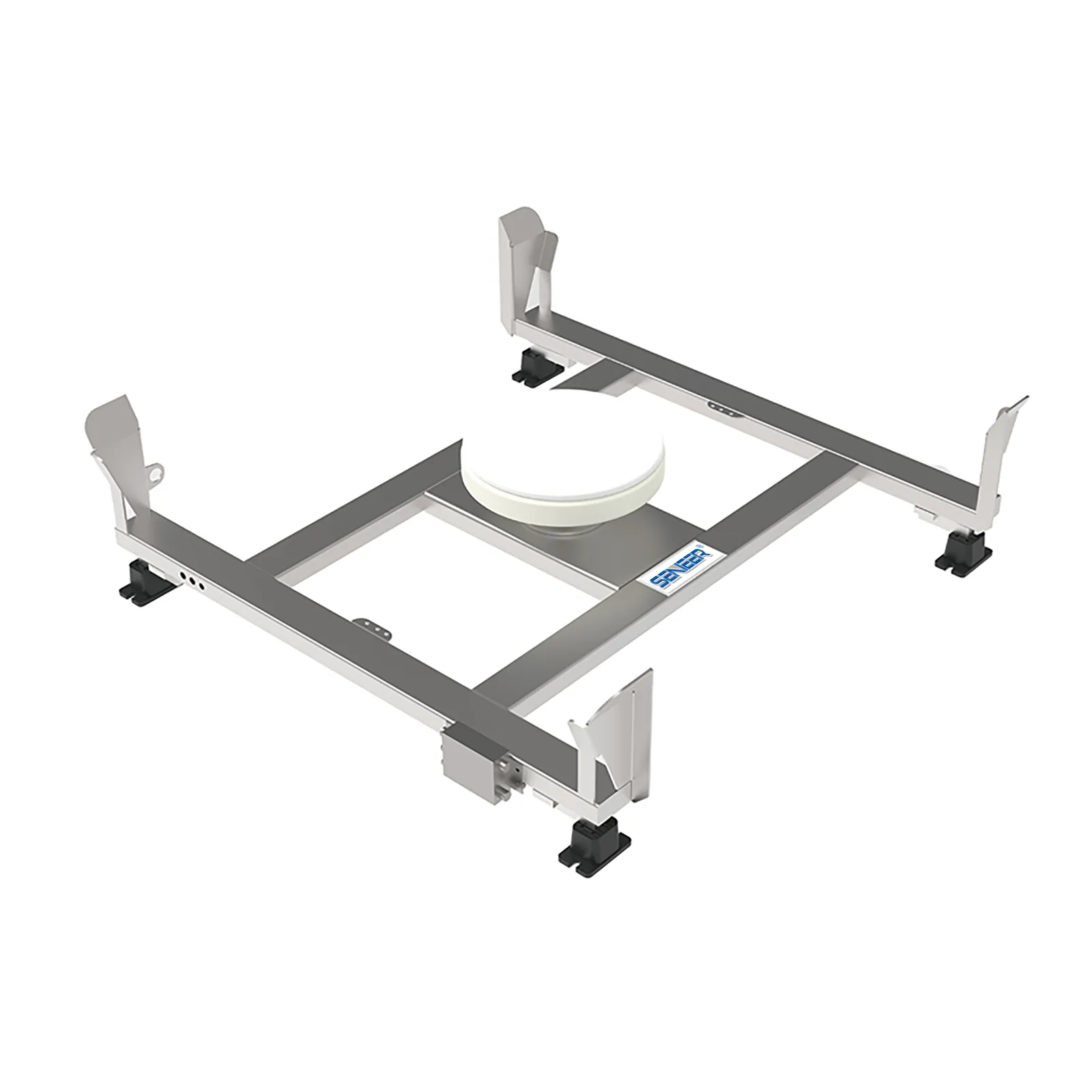
Fixed Station For Cone Valve:
- Assist IBC in receiving materials.
- Adjust the position of cone valve within the IBC, avoiding material leakage.
- Monitor the weight of material filled in the IBCs.
- Optional vibratory function, for compacting materials within the IBCs.
- Used in combination with AGV, achieving factory automation.
- Connect with DCS factory monitoring system.
Vibratory Cone Valve:
- The vibratory discharge cone valve is fixed in the outlet of large IBC, for assistance of discharging material.
- Cone valve can automatically vibrate, interfere with or promote the material flow.
Vibratory Cone Valve - Conical structure, leverage material to flow along the internal surface of valve under the gravitational effect.
- Mode: continuous or intermittent discharging
- Control Lifting and vibrating by compressing air, no use mechanical lifting device, reducing maintenance frequency and not contaminate materials.
- Can control remotely.
Automated Lid-Lifting Device:

- The automated lid-lifting device is installed at the top of fixed station for cone valve, used for automatically remove and replace sealing lid of IBC hoppers.
- The removed sealing lid is stored inside the equipment, which can avoid the dust accumulation on the lid.
- Blow-off function, blow off the surface of sealing lid that is stored inside the IBC hoppers for a long time.
- When the inner and outer pipes move up and down, the lock cylinder is used to achieve relative stationary, ensuring that the material between the inner and outer pipes does not leak out.
- The distance between the bottom of lid-lifting device and the hopper is about 30cm, which ensures the effective lifting of IBC hoppers.
- Chain control with upstream and downstream equipment, achieving the fully automation of AGV conveying IBC hoppers.
Post Bin Blender
Post bin blender is used in conjunction with Senieer cone valve IBCs, to conduct enclosed and dust-free mixing of materials inside the IBC hopper by the way of three-dimensional rotation.
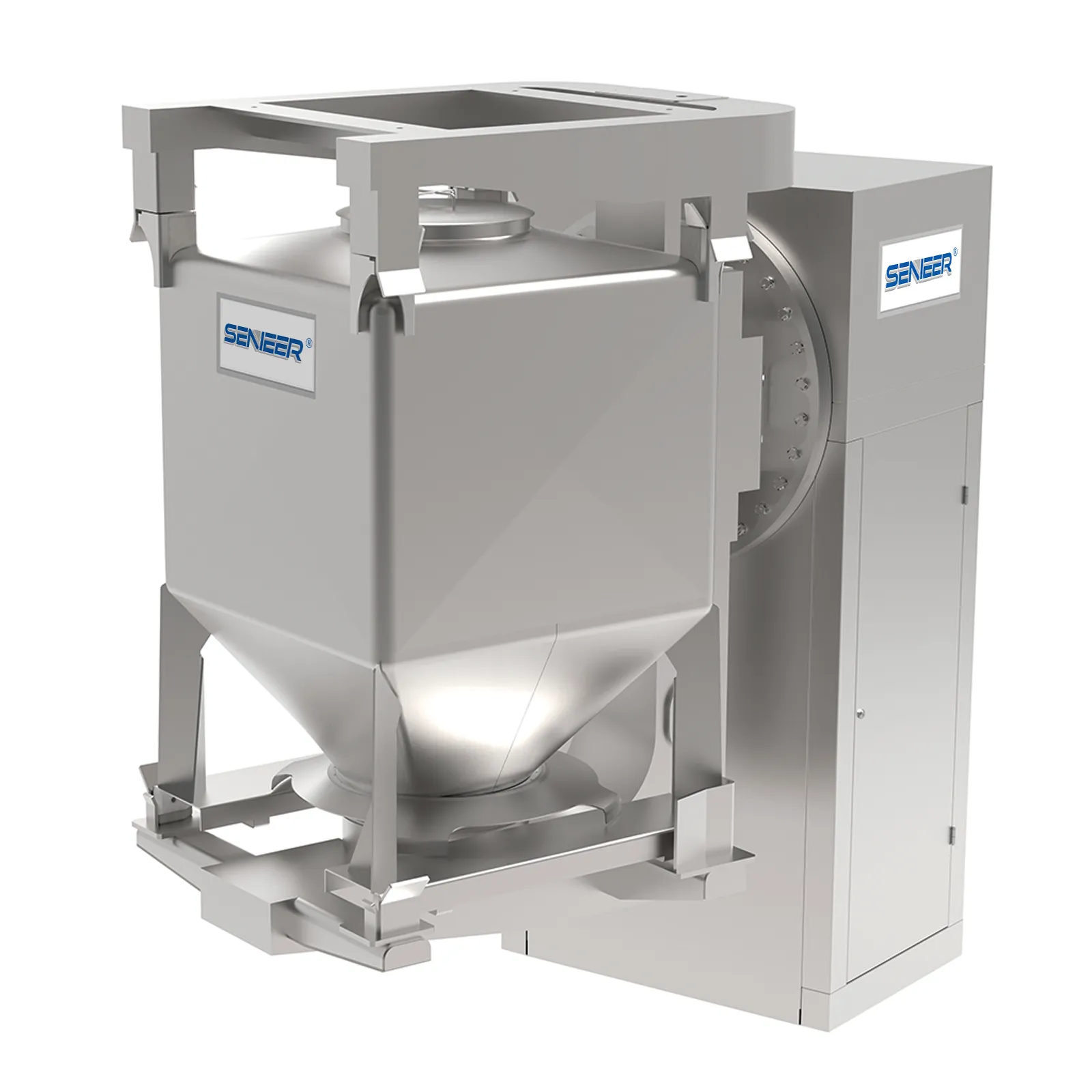
- Post bin blender not directly contact with materials, so it’s zero contamination for the materials inside IBC hopper.
- No need to clean the equipment.
- Consistent and uniform mixing.
- Variable frequency speed adjustment, flexible.
- Be compatible with different volumes of portable IBC hoppers.
- Be used in combination with Senieer fixed station and discharging station, achieving the parallel production processes, enhancing production efficiency.
Cone Valve IBCs
Used for the transportation and temporary storage of powder particles , achieving automatic docking and discharging, and no powder dust leakage.
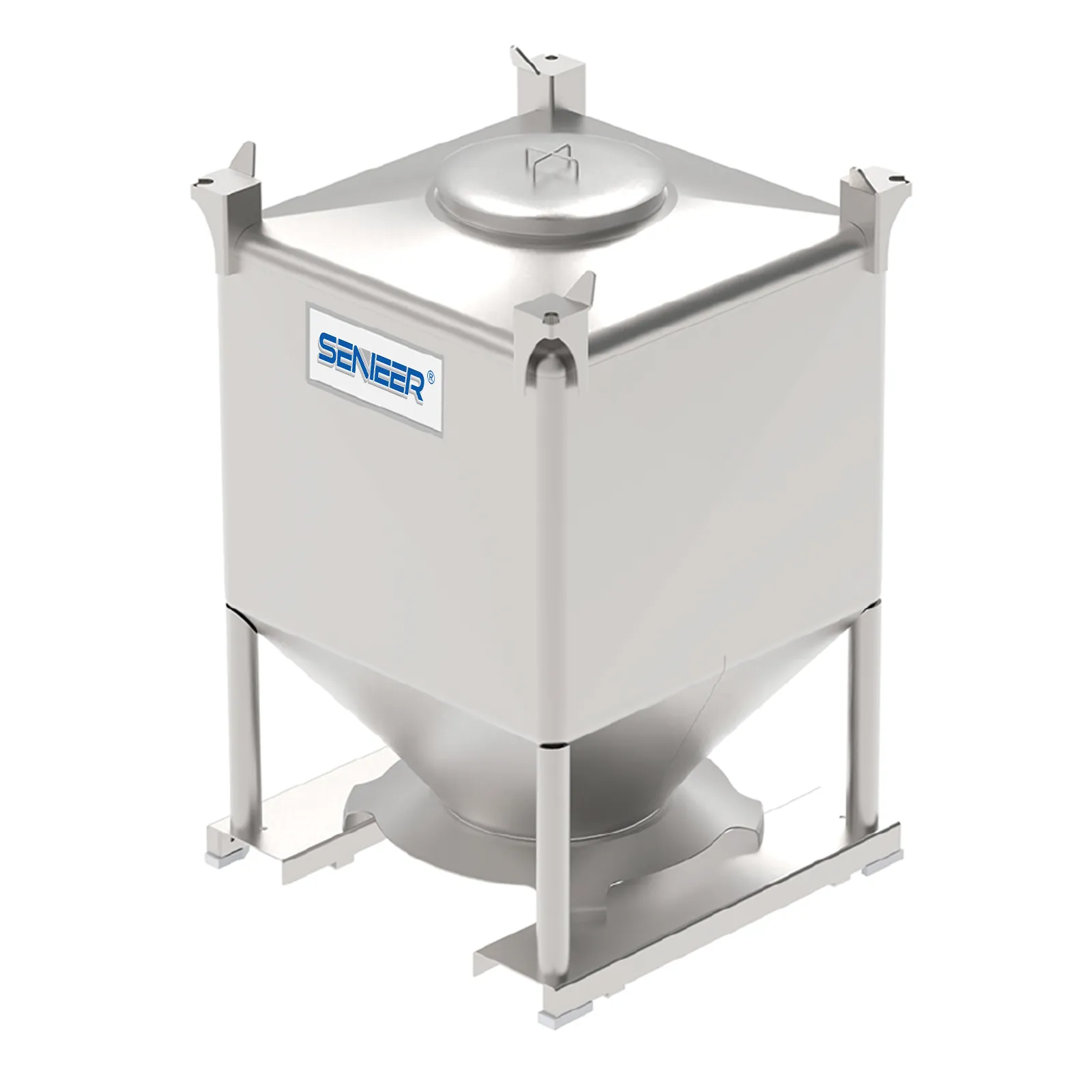
- Can be used as blending container.
- Easy to clean manually or automatically.
- Can be stacked two layers, reduce the storage space for the material hoppers.
- Can be used in conjunction with forklifts and cranes for transportation, coordinate with chain conveyors or roller conveyors.
- The capacity of IBC containers can be custom designed according to client’s requirements, ranging from 300L to 3000L.
Discharging Station
The discharging station in coordination with cone valve IBC to control the discharging of powders and granules within the IBC containers.
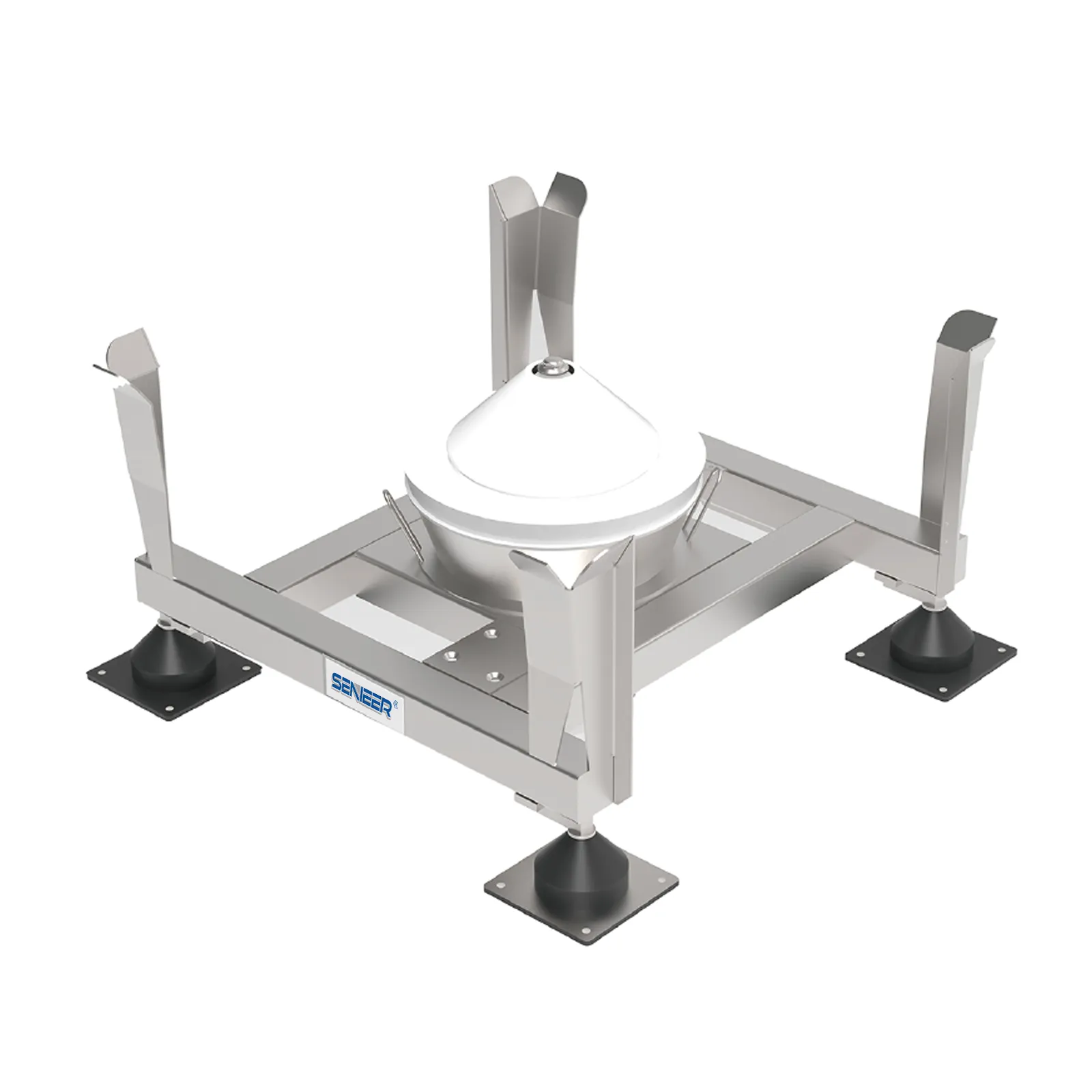
- Monitor the materials inside the IBC containers.
- Enclosed and dust-free discharging materials.
- Inner vibratory function of IBC can enhance the discharging efficiency.
- The outer frames can be equipped with pneumatic vibrator.
- Easy to disassemble for cleaning, CIP or COP.
- Compatible with different capacities of IBCs.
- Optional items: carbon steel frames, weighing units.
Process Comparison Of Cone Valve IBC And Bulk Bag
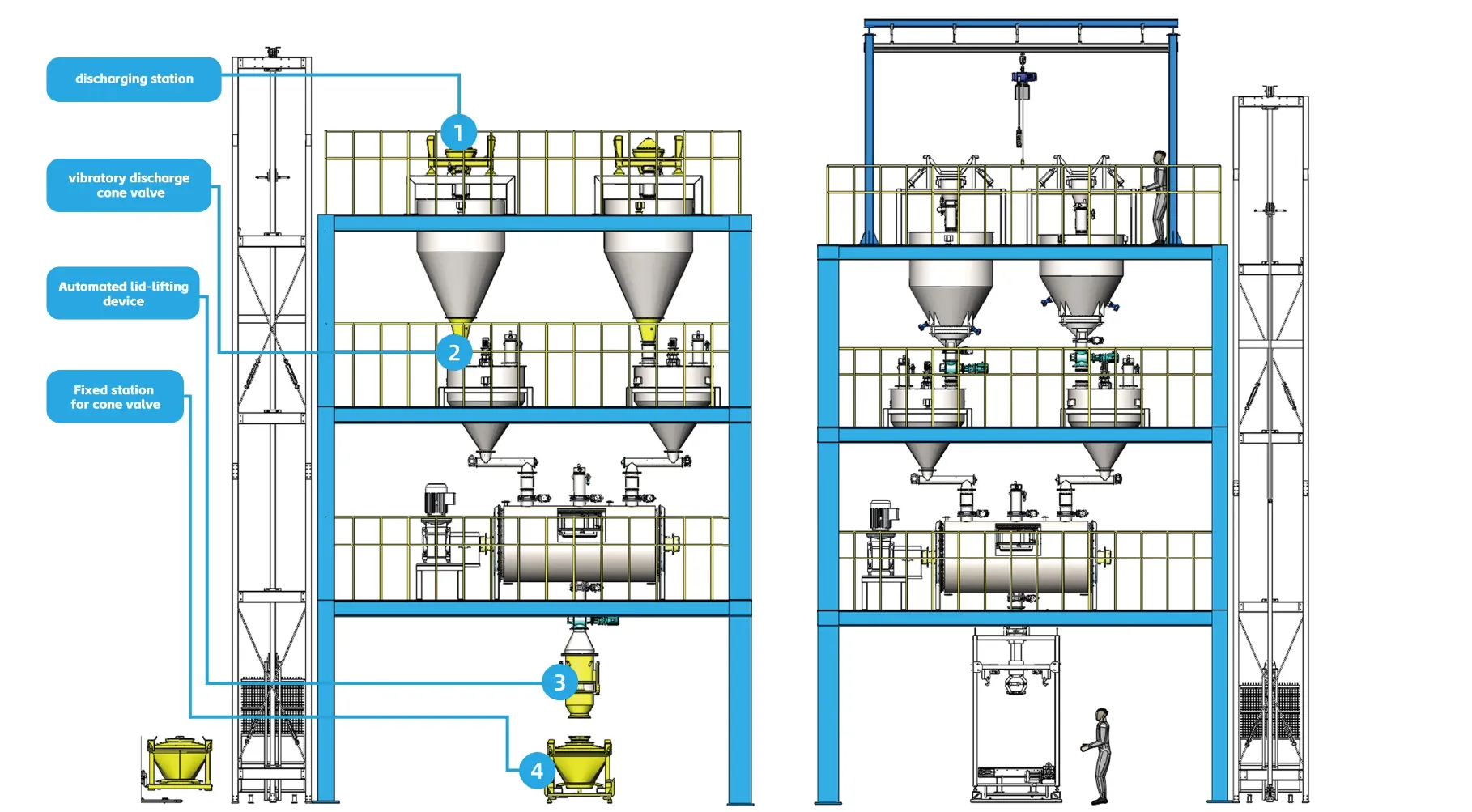
Compared to traditional bulk bag, the process of Cone Valve IBC has many improvements.
Items | Traditional bulk bag | Cone Valve IBC |
Automation | Low | High |
Manual requirement | Frequent | Fully automation |
Consumables | Yes | No |
Sealing property | Low | Strong |
Cross-contamination | Yes | No |
Height requirement | High | Low |
Items | Bulk Bag | Cone Valve IBC |
Structure and design | Filling materials by manual or mechanical; The spatial layout is rather cumbersome. | Cone valve technology; stainless steel IBCs, no dead angle and no residuals, fine polished. Inner structure optimization. |
Operation and automation | Receiving and discharging by manual, easy powder dust leakage; low automation | Fully automatic control including automatic removing lids and discharging. Achieve Unmanned operation in coordination with AGV. |
Material handling | Easily occurs problems of segregation, bridging, rat-holing, etc. Material residuals. | Cone valve technology avoids the occurrence of segregation, bridging, rat-holing and blocking. |
Maintenance and costs | Need to maintain machine support frames and cranes regularly, high maintenance costs. Large occupation, enhances the construction and operation costs. | Convenient maintenance, no consumables and low energy consumption. Takes up less space, stackable of two layers, save the storage space. |
Application areas | Suitable for situations where has low requirements for material handling, or small and medium scales of production for cost-sensitive. | Widely used in pharmaceutical, food, chemical and new energy lithium batteries industries, especially the areas where has high demands for the hygiene, uniformity and automation of materials. |
Applications And features Of Cone Valve IBC
By Senieer one-stop solutions, we can reduce costs and enhance production efficiency for clients. First, it has the function of automatic, dust-free and enclosed filling and discharging materials. Can be used in combination with AGV. Adopts single unpacking stations to serve multiple production lines, achieving automatic docking. No need to add lifting device and require manual work in each production line, achieving the Intelligentization, automation and unmanned operation of factories.
Second, the cone valve IBC process can avoid the destruction and damage of material particle diameters during the transportation process. Third, replacing the traditional bulk bag transportation or pneumatic conveying equipment, effectively reduces the manual intervene and material wasting. Fourth, reducing the energy consumption of factory to reduce the operational costs of factories.
Any questions about cone valve IBC? Welcome to contact us now.
Choose Your Interested Production Line
Bottle Filling Line
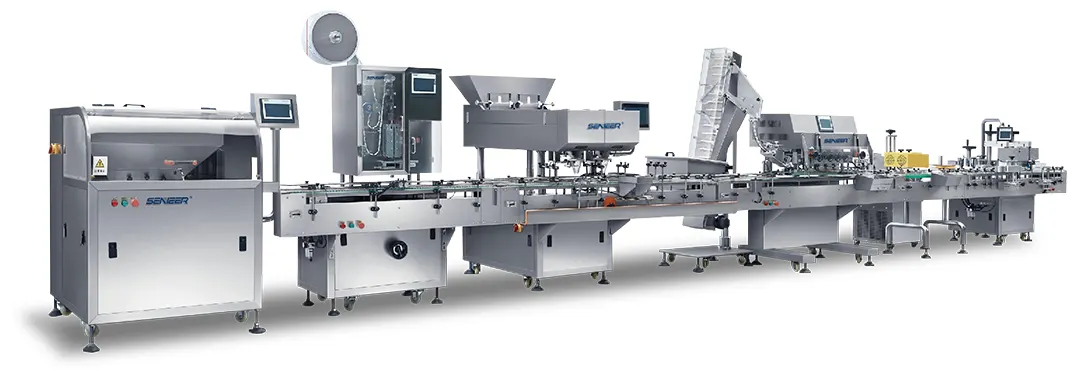
Granulation Line
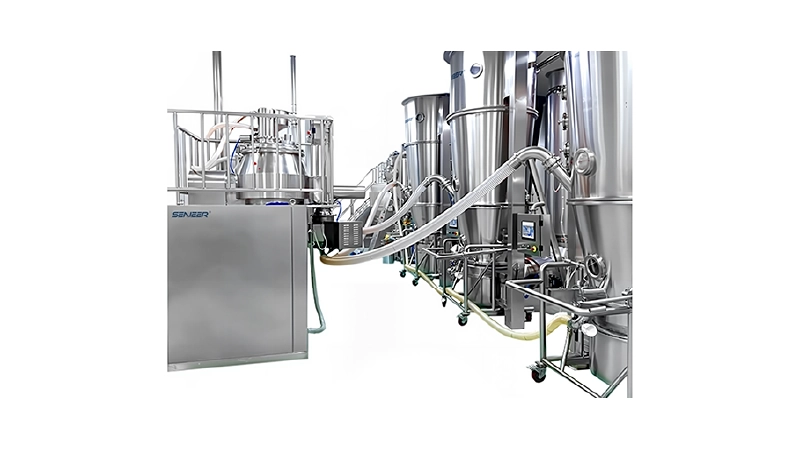
Blister Packaging Line
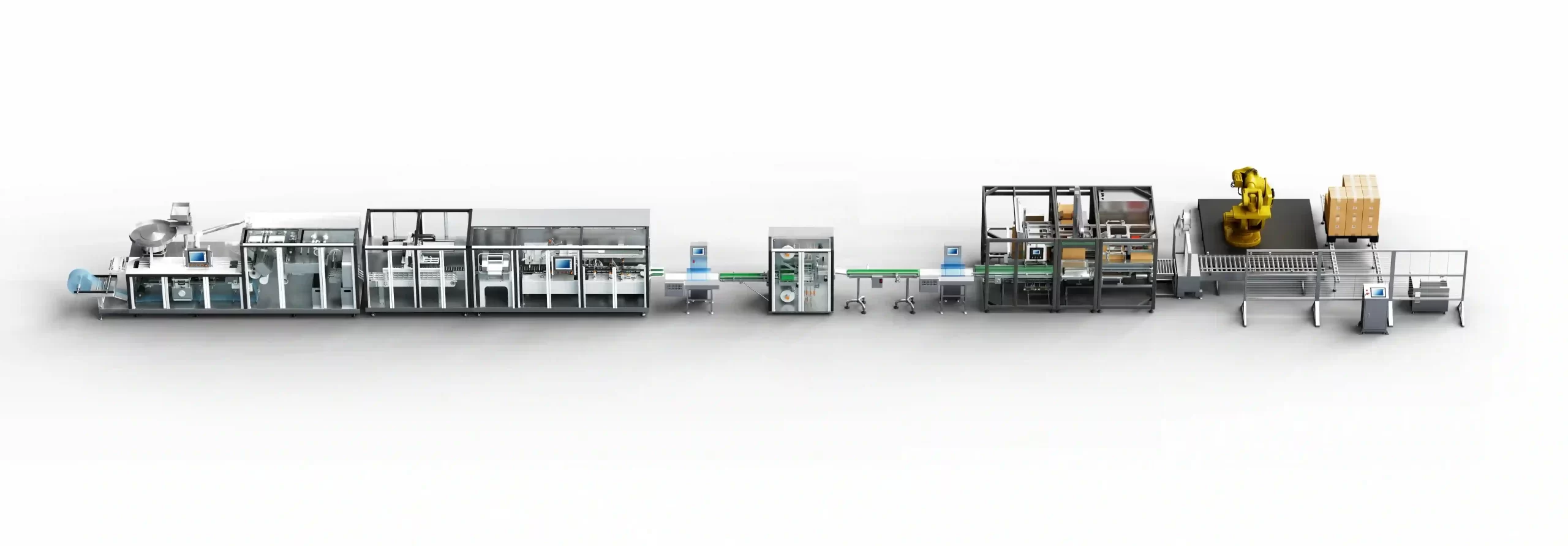
Powder Filling Line
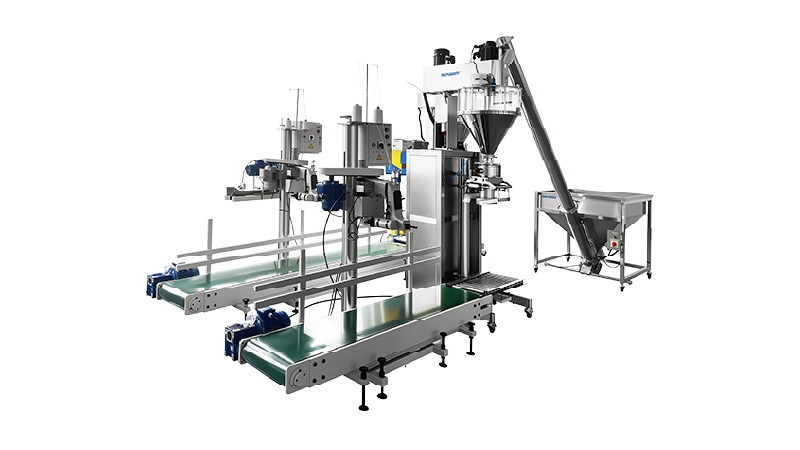