IBC Bin Blender : Product Description
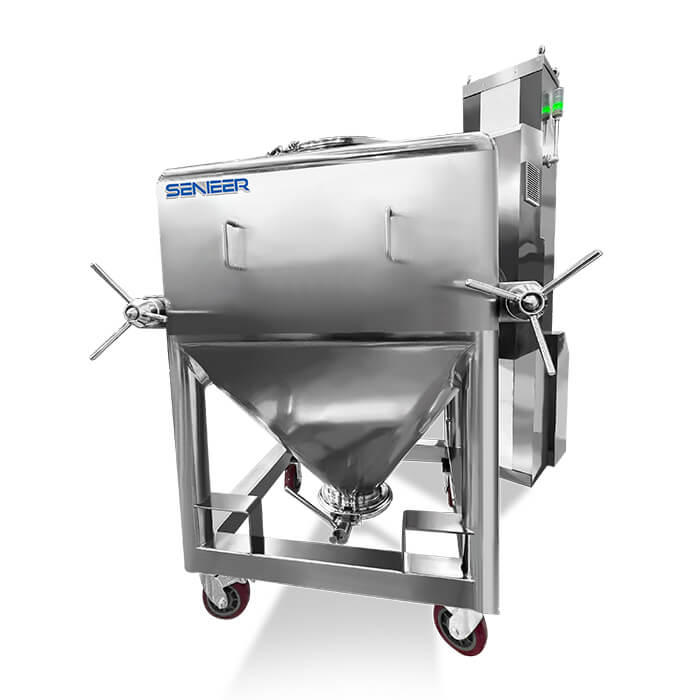
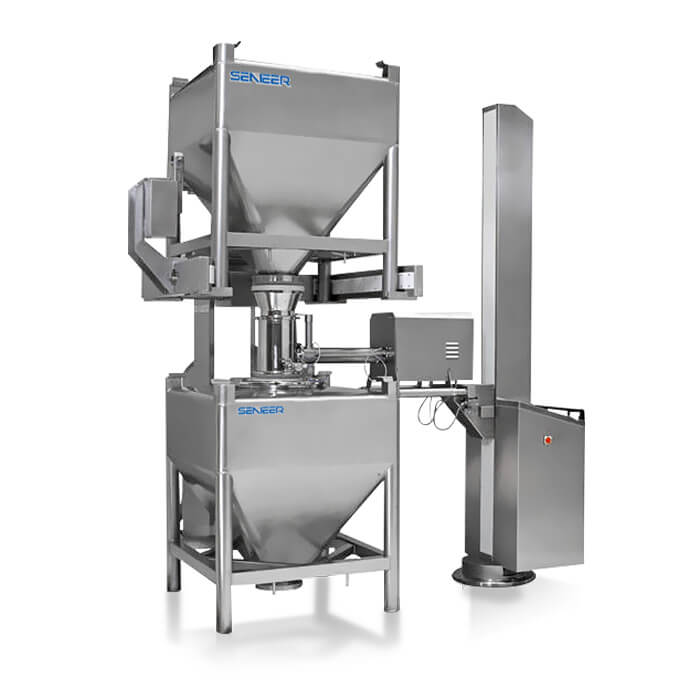
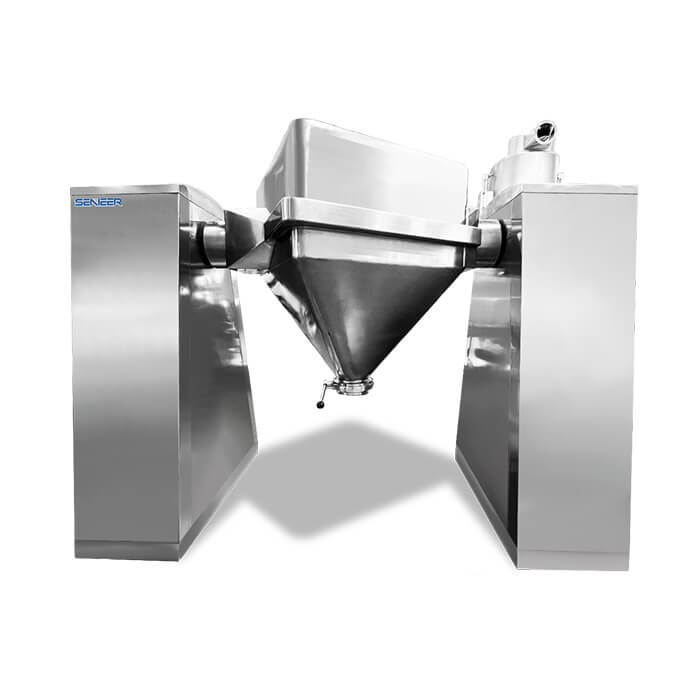
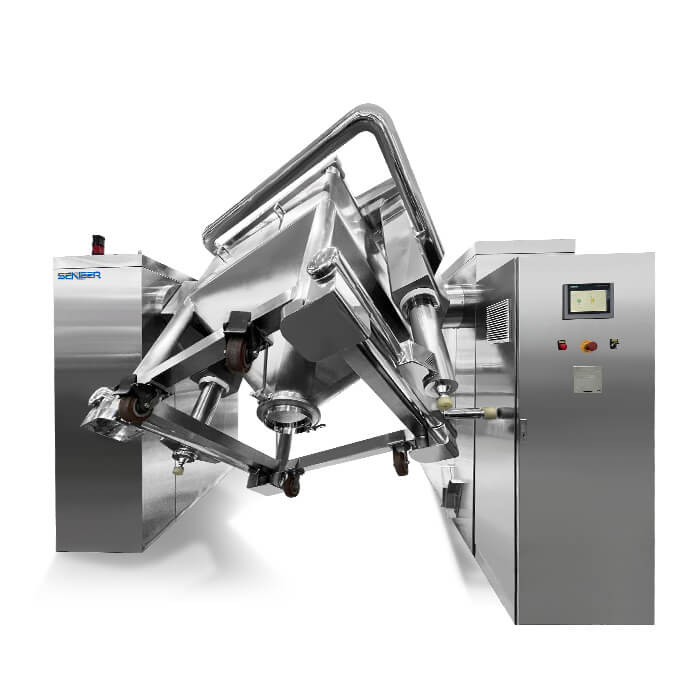
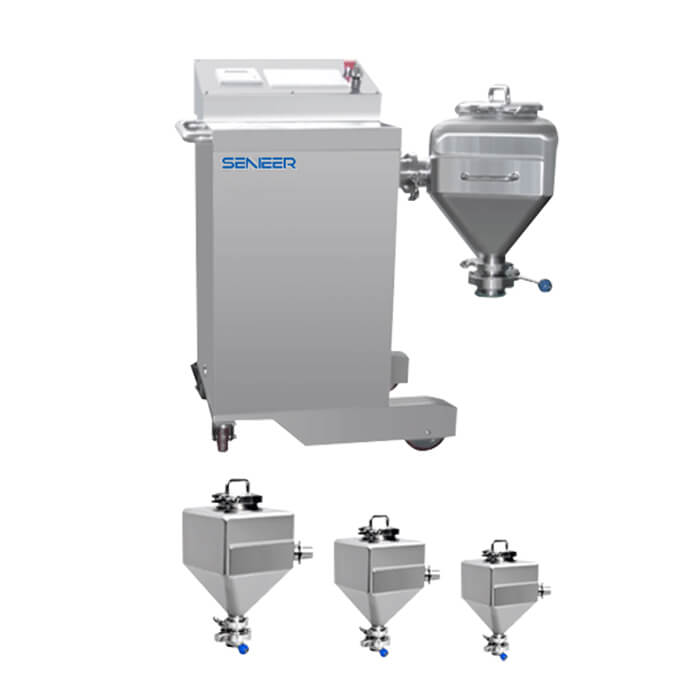
Details of Bin Blender
◈ Bin blender equipped with an infrared safety device
◈ For situations, there’s a built-in safety device.
◈ Pharma bins available in a multitude of sizes and configurations.
◈ Interchangeable bin that can be used for a variety of materials
◈ Stable efficiency, reasonable structure design
◈ The smooth system ensured efficient and reliable production.
◈ Options for registering each product’s operating patterns
◈ Butterfly valve with a constructed safety feature to eliminate false operation.
◈ It provides a variety of safety interlocking mechanisms.
◈ Both the inner and exterior surfaces are all polished to a high standard.
◈ Designed hygienically (utilizes stainless steel for each cover)
◈ No dead angle, no cross-contamination and easy to clean
◈ Ideal to the FDA/ cGMP standard
◈ Blender Bin can automatically complete all actions of the mixing hopper including clamping, lifting, mixing, and lowering.
◈ Blending Bins Manufactured by Senieer are mainly composed of left and right bases, lifting systems, rotary systems, electric control system, and pharma bin.
◈ Senieer has two kinds of Blending Bins, one is posted bin blender, the other one is double base Blender Bin.
◈ Different capacity bins are interchangeable on one bin blender.
◈ Senieer IBC Blender is used in the process required to uniformly blend two or more kinds of powder material in the pharmaceutical, chemical, and food industries.
◈ It is logically structured with reliable and easy operations.
◈ Also, it can be used with IBCs in various capacities to support productivity enhancement.
◈ The blending system fully complies with the cGMP conditions for the production of pharmaceutical products.
◈ From a laboratory IBC Bin Blender or formula blender up to a drum, container or customize blender.
◈ Fully automated, validated blending process with a tumbling movement: By doing without IBC Blender blades, mixers, etc., a blending process could be developed that protects the product and is 100% compliant with hygiene standards.
◈ This involves less cleaning effort and thus contributes to savings in time and costs.
More Models of Bin Blender
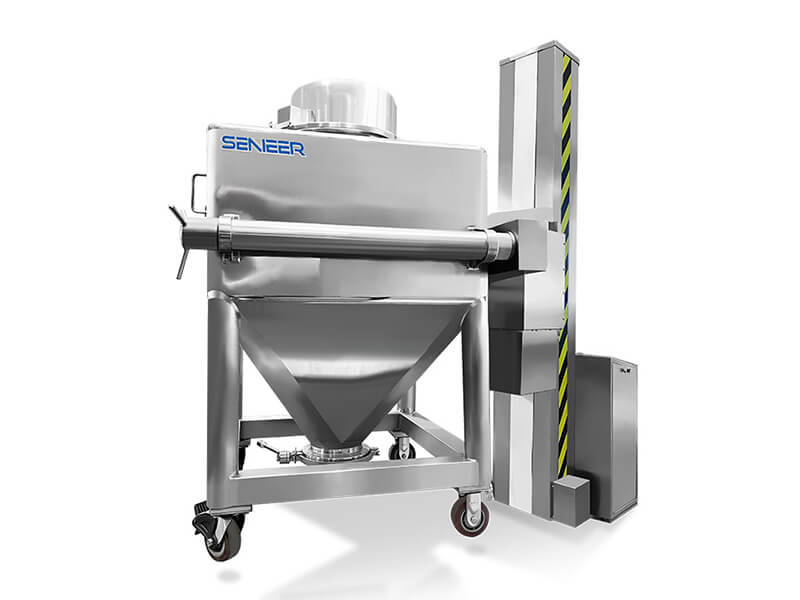
Post Bin Blender
Senieer BCV Series Post Bin Blender is mainly used in solid dosage production for mixing granules with powder. It is ideal mixing equipment for pharmaceutical factories. Senieer IBC blending system structural performance has reached the level of similar international products. It can automatically complete all actions of the mixing hopper including clamping, lifting, mixing and lowering. It’s mainly composed of single column, lifting system, rotary system, electric control system and pharma bin, etc.
The control system will carry out automatic mixing according to the set time, rotation speed and other set parameters. It will also automatically lower to the ground.
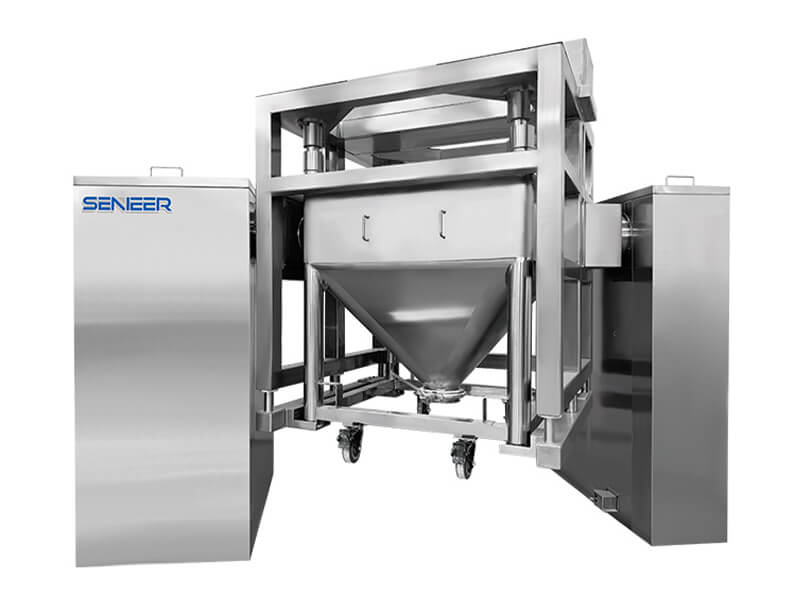
BDV Bin Blender
BDV Series IBC Bin Blender can meet the mixing requirements for large batches and diversified varieties of products. It consists of base, rotary frame, driving system, lifting system and lowering system, braking system and PLC control system. IBC bin blenders with the infrared sensor, ensure safe and reliable production.
Senieer is a premier IBC Blending Systems supplier and manufacturer, custom any IBC Bin Blenders for your detailed application, equipment ideal to the FDA/GMP standard with fully intelligent PLC Control and graphical HMI
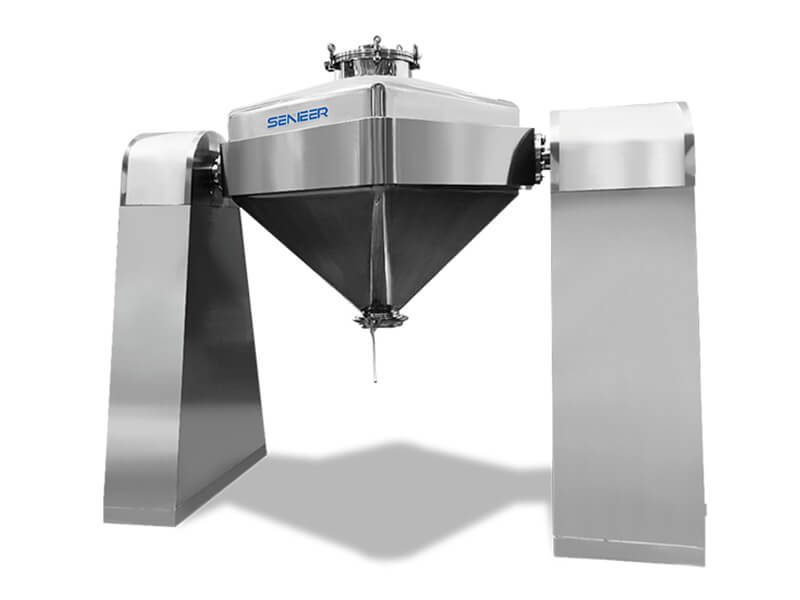
BDN Bin Blender
BDN Series Fix Bin Blenders are widely used in pharmaceutical industry. It has advantage of stable transmission, reliable structure, large mixing amount, and stable transmission. The bin blenders have good prices with trustworthy quality. The printer can print the records according to the set items and process parameters. The highly sensitive infrared sensor device to ensure safety and prevent wrong operation.
Inside of pharma bin smooth without dead corners and mix in a sealed space to avoid dust and cross contamination. The device can also be used to keep the bin smooth and to keep it clean.
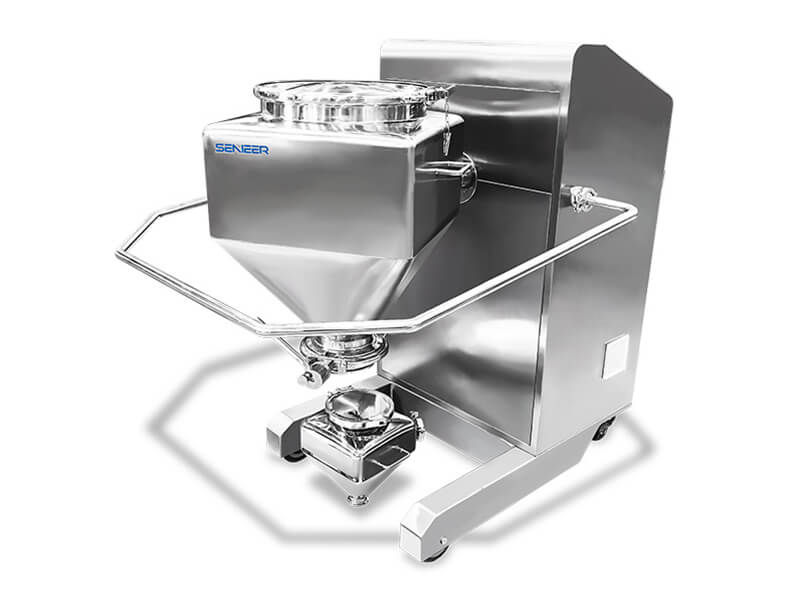
Laboratory Bin Blender
Senieer BSL Series Laboratory Bin Blender is widely used in the solid dosage production, in pharmaceutical laboratory, university laboratory, also used in chemical, food, health food industries. The lab bin blenders adopt the most advanced design, featured by reasonable structure, stable performance and simple operation. Senieer laboratory blenders are easy to use for all material blending processes. The blending bin can realize fast replacement of bins, different volumes and shapes according to your different varieties of materials process requirements.
If you are looking for Bin Blender and custom design your interchange bins, Senieer 33 years engineer team will be here to help you right now.
Any Question About Senieer Bin Blender
Why Global Company Trust Senieer
Top Quality Factory Price
We have a quality control department to verify each product at different phases, from the procurement of parts to finished products
As Your Layout, Customize Machine
According to your layout, we can suggest the best capacity and type for you, customize bin blender for you
Bin Blender Consult & Design Service
Save energy resource for you, professional engineers can improve the best processing solution. Ask us about anything with regards to bin blender and we will answer you
ISO.CE Standard Qualified
We successfully obtaining the ISO9001:2008 certificate and CE security management system certificate. It shows that our bin blender for sale meet the global standards
Bin Blender Training & Maintance Service
Free bin blender training & maintenance service for you, we will provide your team in-depth training on safe operation and bin blender maintenance
Bin Blender Installation Service
Senieer offers bin blender installation & commissioning service for production products, your equipment and control systems are qualified based on the GAMP life-cycle
Bin Blender Ultimate Buying Guide for Importers
Let’s dive right in:
- Chapter 1: What is a Bin Blender?
- Chapter 2: Parts and Components of a Bin Blender
- Chapter 3: Bin Blender Working Principle
- Chapter 4: Features of Bin Blender
- Chapter 5: What Factors Affect the Efficiency of Bin Blender?
- Chapter 6: Advantages of Bin Blender
- Chapter 7: Types of Bin Blenders
- Chapter 8: Industrial Applications of IBC Bin Blender
- Chapter 9: Factors to Consider When Buying Bin Blender
- Chapter 10: Maintenance and Troubleshooting of IBC Bin Blenders
- Chapter 11: Pharmaceutical Bin blender Maintenance Tips
- Chapter 12: Frequently Asked Questions about Bin Blender
- Chapter 13: Conclusion
Blending is one of a series of activities that take place in different manufacturing and processing industries. The process entails mixing and combining ingredients and materials until they form a uniform mixture.
For large-scale applications, a bin blender is used for performing the blending tasks. Are you planning to buy a bin blender in your industry? We have a perfect guide for you.
Read on to learn everything that you should know about bin blenders. We will also broaden your knowledge on how to buy the best bin blenders for sale, including tips on how to choose bin blender manufacturers and suppliers in China.
Chapter 1: What is a Bin Blender?
Bin blenders are equipment that is used for blending dry solid forms such as dry powders which later on will be used for the production of products such as tablets and capsules.
Most bin blenders are irregularly shaped and provide options for charging and discharging solid material into the bin. In most bin blender applications, the materials to be mixed are powder and granules.
The bin blender is properly enclosed and contained to prevent solid particles from finding their way out of the container. The enclosure also prevents the build-up of dust in the room during the blending process.
A bin blender is automated and electric-powered to ensure that it delivers a smooth blending for all the required materials. Most bin blenders depend on hydraulic systems while others have pneumatic power units.
A bin blender is versatile in that it can blend and mix different types of grains and granules. It is also applicable in a wide range of industries starting from pharmaceuticals to the food industry.
Chapter 2: Parts and Components of a Bin Blender
How does a bin blender look like? To answer this question let’s take a look at the key components of the bin blender and the role that each component plays in the blending process.
Here are the main parts that make up a complete bin blender:
Rotation counter
As the name suggests, the counter is designed to implement the rotation action of a bin blender. It is also the component that determines the mixing rate and the blending speed of a bin blender. The counter directly responds to the appropriate settings on the bin blender.
Rotation counters are installed on different bin blenders. However, manufacturers fix bin blenders that will be compatible with their rotation counters.
Driving system
The driving system acts as a bridge between the rotation counter and the blending container. It responds directly to the action of the counter and implements it on the bin blender. The driving system ensures that the actual mixing and blending takes place in the bin blender.
Bin blending container
This is the component in which the actual blending takes place. It is an open container that accommodates the material that you want to blend.
Blending containers come in different shapes, designs, and capacities. They also have different ports and configurations that allow connection with other pieces of equipment.
The container is made of stainless steel metal to sustain all the vigorous activities that come with the blending process.
You may also request a bin blender manufacturer to customize this component so that it can meet your specific industrial needs.
PLC operator control
A programmable logic controller is the main control panel of a bin blender. This is the component that determines the operations and behavior of the industrial blender.
Modern bin blenders are integrated with high-tech operator control features that give you the power to execute a myriad of options. The control features are also user-friendly and make it possible to use the bin blender even if you are not an expert.
The control features of IBC bin blenders are characterized by touchpads and buttons. They also feature minimum sophistication to enhance the ease of using the equipment.
Clamping bars
Clamping bars are fixed onto the bin blenders to enhance the stability of the blending equipment. They ensure that the bin blender will remain balanced despite the vibrations during the blending process.
In some cases, clamping bars are bought as accessories for the bin blenders. They are then welded onto the blending equipment during the installation process.
Charge and discharge ports
The charge and discharge ports act as points of entry and exit on the bin blender. They provide passages in which you can fill up the bin and extrude the material.
The ports are strategically positioned to facilitate the smooth flow of the materials. For instance, the charging port is located at the top of the bin while the discharge port is at the bottom. This arrangement ensures that the flow is by the gravitational process.
Charging ports have different diameter though you can customize according to your requirements. They also have valves that control the inflow and outflow of the materials.
Lifting system
The lifting system of a bin blender elevates the blender to the desired heights. The system is powered by a hydraulic system to position the bin blender upwards and downwards.
The lifting system uses hydraulic technology to execute the lifting and lowering actions on a bin blender.
Chapter 3: Bin Blender Working Principle
How does a bin blender work? To understand the whole working mechanism, let me take you through all the steps through which material is mixed and blended in a bin blender.
Industrial bin blenders operate using the principle of tumble blending. This is among the most advanced methods of blending that guarantees uniform mixing and blending of the materials.
Tumble blending is a method in which the IBC bin blender turns and rotates to mix and blend its content. In this case, we are talking about grains and granules. The rotation is at a moderate speed but is still impactful. The industrial blender has settings that allow the operators to adjust the tumbling speed.
As the blending container tumble, the materials in them are also subjected to the same motion. Individual particles fall and hit each other during the process of tumbling.
The tumbling mechanism of IBC bin blenders is suitable for both light and dense granules and powder. While it is deemed as a gentle method of blending it can also be abrasive hence suitable in the food and beverage industries, where the ingredients have to be blended vigorously.
Tumble blending is also popular because it is easy to control. You can easily adjust the speed of tumbling to get the desired results from the blending process. This explains why IBC bin mixers come with dependable control panels.
Also, this mechanism of the IBC bin blender allows fast blending. With tumbling, it is possible to load large volumes of materials into the bin blender. This means that you can blend several batches of a material within a short time. This is the opposite of traditional ribbon blending which is quite time-consuming.
Meanwhile, here are the procedures for using a bin blender;
Step 1: Charging material into the blender
The very first step of the process entails filling up the mixing container with the required amount of material.
But before you do so, ensure that your IBC bin mixer is clean. It should not have remnants of the previous blend as this can cause cross-contamination.
The volume of the material should be less than that of the blender to avoid overflow which will lead to wastage. However, it should not be extremely less as this may lead to the underperformance of the bin blender. To be safe, just use the manufacturer’s requirement regarding the capacity of the material to be put in the container.
After loading, set the bin blender to a perfect position using a clamp and lifting system.
Step 2: Choose the blending settings
After loading the materials into the IBC industrial bin blender, the next step is to decide the modes of operation. This will determine how the materials will be blended.
One of the important variables that you are likely to adjust at this stage is the speed of blending.
The nature of the materials and your desired output will determine the settings that you will choose for your bin blender.
With modern bin blenders, you can easily enter your settings. The bin blender machines have PLC systems with touchpads that provide a user interface.
Step 3: Stop the blending
You can proceed to stop the blending process once you are sure that your material has achieved the desired blend. The bin blender may stop automatically for the timed blenders since it will not continue operating beyond the period that you had set.
Stop the bin blender and obtain the homogeneous mix through the discharge ports. However, it will be wise to inspect the blend before approving it for the next production stage. If not, return it to step 1 until you get what you want from the blending process.
Step 4: Wash the blender
Once you have finished blending a particular type of material, it is advisable to wash the bin blender until the next phase of blending.
The video below gives a summary of how a typical blender bin works:
Chapter 4: Features of Bin Blender
Before you buy bin blenders in China, here are some of its salient features that you should know;
Available in different capacities
There is no universal size or capacity of bin blenders. They come in different capacities.
The capacity usually ranges between 25kg to 500kg. Within this range, you will find a bin blender that perfectly fits your industry.
The good news is you can still request the manufacturer for a custom capacity bin blender. This is the surest way of getting a bin blender that will accommodate your manufacturing and processing needs.
Dust-free operation and connection
The blending process of a bin blender is completely dust-free. This is to say that it releases minimum dust to the surrounding no matter the type of product that is blended.
This feature extends to the transfer of the materials from the blending to the next stage of production. All the connections to and from the blender are completely sealed to ensure that there is 100% transfer of materials.
Electric control panel
The bin blender features a high-tech electric control panel. You can use this panel to control the cycle time of the blending process.
Whether you would like the bin blender to operate fast or slowly, everything will be within your reach thanks to an efficient and easy-to-use electric control panel.
The bin blender also features PLC controls that have a touchscreen or touchpad this further improves the user interface and usability of the pharmaceutical bin blender.
cGMP bin blender Design
The design of the bin blender is fully cGMP compliance. It fully complies with all the aspects of cGMP that are related to the design of the pharmaceutical equipment.
The design ensures that the bin blender is safe for use and also easy to handle. The design also ensures that there are no dead angles on the container.
Adjustable blending speeds
The bin blenders allow you to blend at different speeds. You can choose to operate at a fast blending speed or you can or the medium and slow speeds.
You will do all the adjustments using the blender’s control panel.
AISI 316 body
The body and metallic components of the pharmaceutical bin blender are made of stainless steel material. This gives the blender maximum strength to support all kinds of blending activities.
The steel metal also guarantees the durability of the bin blender.
Also, the inner and outer surfaces of the bin blender are well polished to achieve maximum smoothness.
Fully automatic
The operation of the IBC bin blender is fully automated. The programmable logic controller on the IBC bin allows you to set the operational parameters. For example, you can choose the rate and speed of blending and through the interface.
Flameproof construction
The construction of the bin blender provides proof against fire damage. It cannot get damaged when exposed to fire and flames.
Interchangeable bins
The good thing about bin blenders is they are easily interchanged. This means that you can easily move from one bin to another during the blending process. This feature also enables you to blend different types of materials.
You only need to pay attention to the specifications of the bin mixer and see whether they can be compatible with the blender to support interchangeability.
Safety mechanism and safety features
Bin blenders are optimized to perform at the highest safety levels. One of the features is the interlocking safety mechanism.
The safety features ensure that both the materials and users are safe during the operations. On the other hand, the butterfly safety valve provides a fool-proof cushion against unsafety operations.
The bin mixer also has an emergency stop button that will bring the operation to an instant halt in case of an emergency.
Quick opening and closing
The charging hole of the IBC bin blender is positioned at the top to allow effortless charging of materials into the bin. It also allows quick opening and closing when necessary.
The bin valve is also strategically positioned to allow easy discharge of the blended materials.
External clamps and connections
The bin blender has clamps that you can connect to other accessories when needed. For example, you can easily connect the bin blender to the trolley to enhance the mobility of this equipment.
Compatible with different bunkers
The bin blender is easily adaptable to bunkers and containers of different sizes. This means that it can easily accommodate different production capacities. Whether you want large-scale or small-scale production. You will simply connect the blender and proceed to blend your materials.
Hydraulic lifting
This blender feature the latest lifting technology-hydraulic power pack system. This one is designed to lift the bin to ensure that you achieve the maximum blending.
Chapter 5: What Factors Affect the Efficiency of Bin Blender?
IBC bin blender is the ability of the bin blender to produce a perfect blend. The best bin blenders are always expected to have high efficiency, even if it is not 100%
However, some factors can make a bin blender to be less efficient. In such cases, the materials exhibit glaring proofs of inconsistencies. You will notice that some particles are larger than others.
Here are key factors that affect the efficiency of the bin blender;
The quality of construction
How your bin blender has been designed and manufactured will directly affect its efficiency. IBC blenders that have been properly engineered are likely to deliver the highest levels of efficiency. This happens because all the components of such bin blenders are characterized by high levels of preciseness.
The blender and the accessories of such bin blender machines will work together towards minimizing operational errors and achieving the best blending.
This is means that the easiest way of getting high-efficiency levels is to buy quality bin blenders.
Cleanliness of the bin blender
The cleaner the bin blender, the more efficient it is. It is just as simple as that. You can make your bin blender perform to the optimum levels by ensuring that it is always in pristine condition.
Cleanliness is more important when you are doing batch blending of unrelated materials. Keeping the blender clean will ensure that the materials don’t contaminate each other.
Cleaning modern blenders is an easy process thanks to automation. You can easily do the cleaning after each batch of the material has been blended. Ensure that all the sections of the bin blender are cleaned, including the hard-to-reach areas.
Mixing process
How the bin blender operates will have a direct impact on its efficiency. The tumbling should be smooth and uniform for an efficient blending.
You may blend for an extended period or at a fast rate but still, get an irregular blend. The problem could be with the execution of the blending process.
It is also important to distinguish whether you prefer batch blending process or continuous blending.
Power needs for the bin blender
This is a key technical factor that determines the efficiency of an IBC bin blender. The blender should be supplied with adequate power for it to function well. However, the supply should not exceed its rated power capacity.
Ingredients for the material
You may still record low efficiency even when using the best bin blender. The main problem could be with the ingredients that you want to blend.
Each material that you want to blend has distinctive characteristics that may make it either suitable or unsuitable for your blender. Some materials have large particles, others have small while others have a combination of large and small-sized particles.
Also, different ingredients have different chemical properties. One common property is temperature variation.
It is important to comprehend the key properties of the materials that you are planning to blend. From there, you can find ways of consolidating them to increase the efficiency of the blending process.
Residence time
This is the time that it takes for the material to be in the bin blender. It has a direct impact on the overall performance and efficiency of the blending process.
Residence time is important both in batch processing and non-stop processing. It is critical to allocate adequate time that will guarantee complete blending of the material. On the same note, ensure that the material does not overstay in the bin blender.
Chapter 6: Advantages of Bin Blender
Are you planning to buy a bin blender but you are not fully convinced? Let’s assure you by outlining the top benefits of bin blender;
1. Homogenous blend
It is easy to obtain a perfect and flawless blend when using the best bin blender. As we have already stated, the working mechanism of the blender ensures that all the particles of the materials are blended with each other.
The high quality of the blend will eventually affect the product that you are processing. It will also be perfect.
2. Fast blending
Are you spending too much time when using your current blender? Maybe it is time to upgrade to the fast and effective IBC bin blender. They are designed for fast blending.
The working principle of the IBC bin blender is capable of blending high volumes of material at any given time. This means that you will be able to complete several batches of the material within a short span. You are also free to increase the blending speed hence save on time.
Despite the fast blending, IBC bin blenders don’t compromise on the quality of the blend.
3. Complete material containment
Containment in this case refers to the ability of the bin blender to accommodate all the materials in it. It does not leave room for spillage which can lead to the wastage of the materials.
This is possible due to the solid construction of the blending container. It is properly sealed and does not have any gaps or holes.
Total product containment also improves the safety of the work environment. It minimizes the accumulation of dust due to the blending process.
4. Prevents contamination of the materials
This is another benefit that comes with the solid construction of the IBC bin blender. The fact that the bin and blending containers are sealed eliminates any possibilities of airborne contamination. The ability to clean the bin blender with ease after every batch helps to prevent cross-contamination.
5. Easy to clean
It is always advisable to keep IBC equipment clean at all times. The good news is you can easily do so with bin blenders. This is possible thanks to the automatic washing system that comes with the most modern IBC blenders.
With such a cleaning system, you don’t have to uninstall the bin blender from its position so that you can do the cleaning. Instead, you can execute the required cleaning activities through the control panel.
6. Strong and durable
Stainless steel tote bin blenders are strong and durable. The steel material of the blender can serve its purpose for a long without breaking or getting damaged by corrosion. In addition to the material, all the components of the bin blenders are embedded in each other perfectly so that they can sustain the vibrations that come with the blending process.
In short, you will incur minimum repair and replacement costs when using a bin blender.
7. Fully automated blending
The operations of the bin blender are fully automated. Once the material has been loaded into the blending container, the remaining activities will be executed automatically. You only need to feed your desired instructions on the blender’s PLC control system.
The main advantage of automation is accuracy and efficiency.
Chapter 7: Types of Bin Blenders
Bin blenders come in different designs and mounting styles. Here are some of the most common types of bin blenders in the market.
1. V-type blenders
This is the most common type of bin blenders that are used for commercial purpose. As the name suggests, they assume the V shape.
The design of this blender type makes them perfect for mixing dry solid dosage materials.
The simplicity of the V design makes them easy to use and maintain. It is also easy to load and discharge materials when using V blenders.
V-type blenders come in different capacities and specifications. You can also place a request for the custom V-blenders.
2. Octagonal blenders
This is quite a unique shape of IBC blenders for sale. The body of the blender has an octagonal shape. However, the top section has a polygon shape.
The irregular shape of this blender improves the efficiency of the blending process. It also makes the blender suitable for both gentle and vigorous blending.
Octagonal blenders are perfect for granular materials. However, they can also be used for powder and fine grain materials.
One of the advantages of the octagonal bin blenders is they minimize wastage of materials. They are also easy to clean.
3. Mass blender
This is another type of IBC bin blender. It is commonly used for mixing dry lumps though it can also be used for wet granules.
This blender has a defined speed and the materials are mixed horizontally given the orientation of the blades.
Mass blender features a dustproof cover to protect the working environment and as well as minimize wastage of the materials.
The automation feature makes the blender capable of blending large volumes of materials.
4. Vertical blenders
As the name suggests, the blades in this blender are vertically oriented. The blender is perfectly suited for blending different types of materials including powder, granules, grains, and even pellets. It is also capable of both dry and wet blending.
It is possible to get a complete discharge thanks to the vertical orientation of this bin blender. These blender types are also easy to maintain.
5. Double cone bin blender
Here, the blenders are characterized by twin cones. This design makes this type effective for mixing a variety of materials.
It can also be used for mixing grains and granules. It is also a go-to choice bin blender for abrasive materials.
The conical design of this blender makes the discharging process easy. Additional features such as a timer improve the overall functionality of this blender.
The design of this bin blender not only improves the usability but also improves the safety of the users when handling.
6. Single column bin blender
This is one of the few bin blenders that support batch blending (Materials are blended in batches). In this type of blending, granules are collected, put in a container, and blended for a defined period before the next batch goes through the same process.
A single-column blender is designed to mix the materials completely without changing the shape and structure of the materials.
The design of this blender supports fast loading and discharge of the materials. It also shortens the cycle time of the blending batches. It also attracts minimum maintenance costs.
Single column bin blender is flexible as it supports different capacities and designs of bins. You can easily use it with both 200 liters and 600 liters bins. It also supports V-shaped and Octagonal shaped blenders.
7. Hydraulic clamping bin blender
This type of bin blender features a hydraulic system for vertical clamping. Powerful and efficient hydraulic cylinders are used on these IBC bin blenders.
The operation mechanism of this bin blender type makes it ideal for use with large bins. It can support bins of up to 3000 liters.
However, safety measures have to be put in place when using this type of bin blender. For instance, ensure that there is no hydraulic leakage.
8. Split fork bin blender
This is just like the other blenders only that it has a different clamping mechanism. The blending bin features cavity lugs that are positioned on two sides of the bin.
It also has forks that are connected to the lugs. It keeps the bin stable and steady during the blending.
9. Twin column bin blender
This type of bin blender has two columns that support the bin. These two have columns have a rotating mechanism which is affected the bins containing the materials.
Given the design, the blending process of this blender is diagonal. This is different from other bin blenders in which blending is central.
The heights of the bin can be adjusted through different heights along with the twin columns.
Chapter 8: Industrial Applications of IBC Bin Blender
To know the uses of IBC bin blenders, take a moment to critically look at your products. Do you think their quality will suffer because of inadequate mixing or blending process? Away from your company, look at the products from other industries, especially those that are made from different ingredients. Imagine how they will be if there was no mixing.
From your brief analysis, you must have realized that most products that we depend on are a result of elaborate blending and mixing. Remove the IBC blending process and we will be having inferior products in the market.
This is just to tell you that IBC bin blenders enjoy a wide range of applications. Here are some of the sectors that heavily depend on bin blenders.
Pharmaceuticals and Bio-tech industries
This is an industry that mainly deals with the manufacturing and selling of drugs. Usually, drugs are a combination of different ingredients which are mixed to form a potent substance.
IBC bin mixer provides an innovative solution for mixing and blending different materials that will be used for making medicines.
IBC bin blenders meet the strict standards that are required for medical equipment, including the FDA and cGMP. This is in addition to other tight regulations that guarantee the safety of the drugs and related products.
If you are in the biotech, medical or pharmaceutical fields, you will find bin blender an important asset.
Food and beverage industry
Food and beverage are big industries that rake in billions of money across the universe. Companies in this industry use IBC equipment for mixing and storage of the ingredients. Bin blender is among the most common equipment that is used for the production and processing of food and beverages.
With IBC industrial bin blender, it is very easy to observe high hygienic standards that are required in this industry. This will contribute to the safety of the products. The precise and complete mixing in the IBC bin blenders also improves the quality of the final food and beverages.
Chemical industry
Well, mixing tends to go hand in hand with chemical processing. Different ingredients of chemicals have to be mixed and blended. No equipment can do this job better than the blender bin for chemicals. Walk into any chemical processing plant and you will not fail to find this equipment.
One thing about chemical processing is it presents a unique set of challenges that require special equipment. For example, some chemicals are toxic when exposed to the atmosphere. The air-tight construction of the stainless steel tote bins prevents such exposure.
Also, some chemicals are corrosive. They can easily corrode the IBC bin blenders causing physical and structural damage. Stainless steel tote bins provide a perfect cushion against such damages.
Agriculture
Agriculture is another major industry where bin blenders are heavily used. A variety of agricultural products have to be mixed properly during processing.
Bin blenders are used for mixing chemicals for pesticides and parasites. These products will then be used for treating and protecting animals against the effects of pests and parasites. Also, the bin blender can be used for mixing soluble food solutions that animals consume.
The same applies to crop farming. Chemicals for protecting crops have to be mixed in the blender before they are used on the farm.
Water treatment
The process of water treatment also involves mixing various products and even chemicals that are designed to kill toxic substances in water. The design and construction of bin blenders make them ideal for this process.
The fact that you can get large IBC bin blenders for handling large volumes of water makes things better. It increases your capacity to treat and recycle large volumes of water at a time.
The best IBC stainless steel blenders are perfectly designed for the storage of soiled and contaminated water making them reusable. The stainless steel material for the bins prevents physical damage due to rust and corrosion.
So, if you are planning to set up a water treatment plant, you may consider getting quality bin blenders for sale.
Oil and gas production
IBC bin blenders are heavily used in the refinery of oil and gas. The blenders provide an enclosed compartment where all the required mixing can take place without having any negative impact on the surrounding.
Also, the stainless steel tote bins are designed to safely handle the blend without compromising the quality of the products from the oil refinery. Also, the non-reactive nature of this equipment increases the safety of the oil mixing and production process.
Cosmetic industry
Companies that belong to this industry specialize in making products for use by people. These products include skincare products or hair products.
Proper mixing and blending should be done to ensure that the final cosmetic product is 100% safe and efficient. And this is where the importance of bin blender comes in.
Apart from being efficient when it comes to mixing, bin blenders help cosmetic companies to observe high levels of sanitation. They are easy to clean and this will ensure that the final product meets high hygienic standards.
Are you planning to get into the cosmetic industry? Contact us for the best deals for the bin blenders.
Paints and coatings
Companies that manufacture paints and coatings require IBC bin mixers for the best mixing process. This is vital given that paints are a combination of different ingredients and components. For example, the coloring agent on paints must be mixed with other chemicals to achieve the desired hues and texture.
Chapter 9: Factors to Consider When Buying Bin Blender
Before you buy an IBC bin blender in China, it is vital to put these factors into serious consideration;
1. The type of bin blender
We have already seen that there are different types of bin blenders. Each type comes with its unique design and even mode of operation.
Also, some types are more applicable in a specific industry and not in others. So, you should consider the type of bin blender that will meet your processing needs.
Try to understand whether you need a hexagonal bin blender or a V-shaped bin blender for your application.
2. What is your bin blender application area?
What do you intend to use the bin blender for? The answer to this question will determine the detailed specifications of the bin blender that you should buy.
Whether you are in food, chemical, pharmaceutical, or any other industry, you should buy a bin blender that will perfectly fit your application area.
The nature of your industry and products may also dictate the type of bin blender that you should buy.
3. Bin blender capacity
You need to decide on the ideal holding capacity of the bin blender that you want to buy. This is the volume of the material that the bin blender can hold at any given time.
Bin blenders are usually calibrated in liters. The volume of the bin blender that you choose to buy will depend on your production capacity.
If you have a high production capacity, you may opt for the large bin blenders for sale. Medium-size bin blenders are ideal if your production capacity is not very high.
Bin blender manufacturers know that no one size will fit all your requirements. To solve this problem, they design multiple bin blender sizes for different users.
Also, manufacturers give buyers options of asking for custom-size bin blenders.
4. Bin blender settings available
Most bin blender manufacturers allow users to adjust the operational settings of their bin blenders. You can change the speed and power input of such bin blenders.
Other bin blenders come with fixed settings and you won’t have to change any settings.
The option of changing the settings comes in handy especially when you intend to blend different types of ingredients. Some materials require high-speed blending and others slow. Some require high power and others low or standard power.
The user interface of most benders comes in the form of buttons and a touchpad where you simply need to punch some settings and it will operate the way that you want. High-end bin blenders have touchscreen features that act as their user interface.
Some settings will even allow you to select the type of material that you want to blend.
Do you want more control options on your bin blender? It will be prudent to talk to the manufacturer for customized settings.
5. Is the bin blender easy to clean?
Regardless of your application area, the cleanliness of the blender will always be paramount. You will always have to clean the bin blender after every single use.
But the nagging question will always be; is the bin blender easy to clean?
You don’t want to waste a significant amount of time cleaning the bin blender or buy a bin blender that will require you to deploy specialized labor or systems to get the cleaning job done.
Find out whether the bin blender comes with any high-tech cleaning aids. One of them is the CIP/WIP cleaning system that cleans the bin blender automatically.
The design features of the bin blender should also make it easy to handle the pharmaceutical equipment when you intend to clean it manually.
Do not forget the exterior of the bin blender in terms of the ease of cleaning. It should be relatively smooth and devoid of crevices that will give you hard time when you do the cleaning. Polished external surfaces are easy to wipe and clean.
6. Sealing
The blending process should take place in a well-enclosed container. Does the bin blender have an air-tight sealing?
Inspect the bin blender to ensure that it does not have any cracks or holes that can lead to the leakage of the materials.
Also, check the functionality and compatibility of the lids. Ensure that they fit tightly and perfectly on the bin blender. This is a vital feature since most bin blenders come with removable caps and lids.
Apart from minimizing wastage of the materials, the lids also prevent cross-contamination that can occur when the unwanted materials find their way into the bin blender.
A properly sealed bin blender also prevents air pollution as a result of dust leaking from the bin blender during the blending process.
7. Do I have enough space for the bin blender?
Apart from the volume or capacity of the bin blender, you should also be concerned about the availability of space in your facility. Will there be enough space in which the bin blender can fit perfectly?
There should be enough space that will allow you to operate the bin blender without compromising your safety.
The room in which you plan to keep the bin blender should be spacious enough to allow movement and transfer of the materials.
8. What accessories do I need?
Find out if the bin blender that you are planning to buy comes with some accessories or whether you will have to buy them separately.
Tools such as trolleys and clamps improve the efficiency of using the bin blender. The IBC bin blender manufacturer may also advise you whether there are other extra compliments that you need to buy for the bin blender.
9. Bin blender warranty?
Buying a bin blender in China is a major investment that you cannot afford to overlook. After spending a significant amount of money on such a piece of equipment, you should have peace of mind that the pharma equipment will serve you well. This is where the issue of warranty comes in.
Find out whether the bin blender comes with warranties. Do not stop there, go ahead to inquire about the conditions of the IBC bin blender warranties.
Proceed to buy the bin blender for sale only after you are fully satisfied by the above factors.
Chapter 10: Maintenance and Troubleshooting of IBC Bin Blenders
Like other machinery systems, bin blenders won’t operate smoothly forever, no matter how good quality it is. Some problems can slow the production process and even stop.
To help you get over such situations, we have compiled a list of the common bin blender problems and their solutions.
Overflow of the materials
This is a basic problem that you are likely to experience when the bin blender is filled to the brim. An overflow can lead to immense loss. The best way of solving this problem is to load the bin blender with the required volume. Do not exceed the bin blender capacity.
Bin blender does not blend
After loading the bin blender and turning it on, it does not respond. This means that no blending takes place. The first thing that you should check is the power supply. Verify whether the industrial blending machine is receiving the required power.
If there is nothing wrong with the power supply, then you may have to open up the blender to inspect some internal blending components. For instance, you can check out for a problem with the motor.
It is advisable to hire an expert bin blender technician to solve this problem.
The bin not filling up
Usually, the material from the blender is supposed to fill up the bin. However, this may still fail to happen.
The first way to diagnose this problem is to check whether the blender is functional. You can also check the material to see whether it is suitable for the blending process. Ensure that there is a smooth connection between the bin and the blender.
Turbulent dispensing of the blend
We usually expect the material to be dispensed smoothly from the blender. Erratic dispensing is a sign of a problem that you need to solve. Check out the air chamber to find out whether the passage has been clogged or blocked.
Improper blend
The blend from the bin bender is usually expected to be smooth and uniform. However, cases of improper blends are quite common. Various factors can contribute to this problem. The bad state of the motor could be the main cause of the improper blending. You may also check the blades of the blender to ensure that that they are in perfect condition.
Screeching and squeaking noise from the bin blender
After using your IBC bin mixer for a long, you are likely to hear sharp noise whenever it is in operation. The sounds are probably due to the frictional force between the moving parts. Some parts could be worn out and need immediate replacement. This problem may also require an experienced person to check out and solve.
In summary, you may experience some issues with your bin blender pharmaceuticals. It is always advisable to have an experienced technician in place to solve the issues.
It is also important to follow the manufacturer’s manual when trying to solve any bin blender problem.
Chapter 11: Pharmaceutical Bin blender Maintenance Tips
After buying an IBC bin blender, it is obvious that you would want it to serve you for a considerably long period. The secret to achieving this goal is by maintaining it well.
Let’s look at some of the effective tips for bin blender maintenance;
- Bin blender cleanliness:Ensure that the bin blender is always in pristine condition even when you are not using it. Do both the internal and external cleaning of the bin blender. Remove traces of stains and dust.
- Check all the connections:Inspect all the connections to and from the bi blender. Ensure that they are not worn out or broken. The inspection should also include the positioning of the cylinders since they might have been affected by the vibrations of the blending process.
- Mixing chamber:Inspect the mixing chamber of the bin blender to ensure that it does not have any foreign materials.
- Test the valves:Inspect the valves regularly to ensure that they open and close easily. You should also be keen to find out signs of wear and tear on the bin blender.
- Don’t overload:Do not fill up the bin blender beyond its recommended capacity. This may cause some strain and even damage critical parts of the bin blender.
- Use original parts:when it comes to the replacement of the bin blender parts, ensure that you use original parts from the manufacturer. The parts should be compatible and not cause any technical issues.
- Manufacturer’s manual:Use instructions from the manufacturer when using the bin blender. In case of any issue, contact the manufacturer for clarification.
- Professional technician:Hire a qualified and experienced bin blender technician for help when it comes to troubleshooting different problems.
One paramount issue that you cannot ignore when it comes to IBC blender bin maintenance is the quality of the equipment. There will be fewer problems and breakdowns when you buy quality bin blenders in China.
Chapter 12: Frequently Asked Questions about Bin Blender
Do you have any questions about IBC blenders? Take a look at some of these frequently asked questions about this equipment. Probably yours is among them.
What is the bin blender used for?
The primary function of the bin blender is to mix grains and granules. It is also used for mixing powdery materials.
When it comes to real-world applications, bin blenders are used for mixing filling materials for the capsules. In the process of mixing, it creates a homogenous mixture. This simply means that the resultant product from the blending process will have the power of each ingredient.
What is blend uniformity and how can I achieve it?
Blend uniformity is a key parameter that is used for measuring the effectiveness of a bin blender. It gauges how uniform the materials of the IBC bin mixer will be mixed and blended.
It is important to verify the uniformity of the materials after each blending process. Also, when buying your bin blender, find out how its operations will affect its uniformity.
cGMP requires that pharma manufacturers test each batch of the products to test various parameters, among them is the uniformity and homogeneity of the blended materials.
Various factors affect the uniformity of blended material. They include;
Particle size
Since blending may involve the mixing of different ingredients, in most cases, the sizes of their particles are also different. Some ingredients have large particle sizes while others have small.
This can end up affecting the uniformity of the materials even after the blending process. This is usually the case when there is a big difference, otherwise, it is easy to minimize the impact when the difference in size is small.
Non-optimum blending
This is a problem when the bin blender is not programmed to operate to the optimum levels. In such cases, you are likely to record underperformance from the blender.
Weight difference
The varying weight of the different ingredients can also have a direct impact on the uniformity of the blended materials. Just like the size issue, you need to consolidate if the weight difference is big. You should probably put in place an effective weight control measure.
Density difference
A significant difference in density is also likely to affect the uniformity of the materials. This is likely to happen because the materials of higher density will be segregated from those of lower density.
Inadequate particle distribution
If the particles are not well distributed during the blending process, there will be a high chance of failing to achieve the desired uniformity. Here you should analyze the effectiveness of the bin blender to ensure even distribution of the materials.
Sampling and analytical errors
This mistake is likely to occur during the process of sampling the materials for the blending process. A mistake made at this stage is likely to affect the uniformity of the final blended materials.
How do I improve the uniformity of the bin blender?
There are various techniques that you can use to keep the blended materials uniform.
The first step to ensure that you minimize the analytical and sampling errors. Follow all the required procedures that should be performed at this stage.
It will better to observe proper timing for the blending process. Ensure that adequate time is accorded to the process so that all the ingredients and particles mix thoroughly to the required levels.
Choosing the best industrial bin blender can help you achieve the desired uniformity. It will be easy to optimize the blending process when you have the best equipment for doing the job.
Why is the mixing time of the bin blender important?
Mixing time is one of the key parameters that affect the operations of the IBC bin blender. This is the duration taken for the materials to be blended.
As an operator, you are required to strictly observe the mixing time. Under timing can result in partially blended materials.
On the other hand, blending beyond the required time can lead to segregation and disintegration of the materials. This can lead to the unequal distribution of the ingredients.
Take time to study the requirements of the materials and choose the ideal mixing time. A well-timed mixing process will result in quality end-products.
Also, mixing time can affect the uniformity of the material. Since the blending process involves mixing different ingredients, the structural and chemical differences between these ingredients could prevent the final mixture from being uniform or homogeneous.
What is segregation in blending?
Segregation, which is commonly known as demixing is another issue that you are likely to encounter when using a bin blender.
The problem can occur when blending either powder, grain, and granule materials. Segregation is likely to result in undesirable outcomes from the blending process.
Demixing inside the blender
Various scenarios can lead to the occurrence of segregation. It can occur inside the blender, in the bin orb during the process of discharging materials from the blender to the bin.
The nature of segregation inside the blender may depend on the type of blender that you are using. For the v-blender, segregation is likely to occur when the blender is rotated on one axis at slow speeds.
The tumbling of powder can easily cause the materials to segregate on the axis of rotation. At the end of the blending process, you may notice that the materials have different axial bands and different particle sizes.
Connective bin blender has a reputation of minimizing the intensity of segregation unless the materials accumulate on the dead spot of the blender.
The discharge stage is another scenario that can cause segregation of the blended materials. This happens when the materials flow downstream to the blender bin.
This segregation is known as sifting segregation as the smaller accumulate to form heaps. Larger particles will form in the middle of heaps instead of rolling down the heap.
You will notice segregation further when transferring the materials from the bin mixer to another container for further processing.
Segregation during the sampling process
In this scenario, a piece of equipment known as a thief sampler is used for extracting a sample of the material from the blender. The equipment is designed to obtain materials from the bin blender without interfering with the structural features of the powder.
However, the process of dragging the sampler from the blender can easily lead to segregation or demixing.
How to minimize demixing in blending?
Whether you are blending for pharmaceutical, food, chemical, or any other industry, it is vital to put adequate measures to minimize the effects of segregation. Here are some effective tips that you can use to reduce the segregation of the materials in the bin blender;
Find out the cause
The surest way of dealing with a problem is finding out its primary cause. As we have explained, different factors can cause demixing.
Find out whether the problem is caused by different particle size, density, or the type of bin blender. You can do the diagnosis by testing a small sample of the material to be blended.
Examine the bin blender
Another solution is to carefully examine the working and operation of the bin blender. Find out any mechanical and electrical issues that may be affecting the normal operations of the bin blender.
The bin blender should be in perfect working condition.
What is a V-type Bin Blender?
While looking for an industrial bin blender, you are likely to encounter one unique blender; V blender.
As the name suggests, this is a V-shaped blender that blends products through the rotation mode. As the blending container rotates, all the materials are evenly mixed. This blender also takes a significantly short time to mix the material.
The body of this bin blender comprises of two cylinders that are inclined next to each other to form a V-shape. The inclination is at a special angle, and in most cases is between 70 to 100 degrees.
However, the accuracy of a V-shape bin blender heavily depends on the volume of the material in it. It is not advisable to fill up this IBC bin blender to the brim. Instead, you should only have it 60% full.
Despite having a unique shape and design, V-shape bin blenders are easy to use. Once you have loaded the materials in the blender, you simply need to set it and it will start the mixing process. Once the blending period is over, you will easily discharge the material.
They are also easy to clean. As all the components are easily accessible.
What is the difference between Bin Blender and a V blender?
Which one should I buy between an industrial bin blender and a V blender? To help you make the right choice, we have outlined key differences between these two types of bin blenders.
Bin Blender | V Blender |
It is easy to customize the shape design and configurations of a bin blender to meet your manufacturing needs. This is why bin blenders come in many different shapes. | It is not easy to customize a V blender. You buy when its two cylindrical containers have been joined at a defined angle (60-75 degrees) |
Bin blender is easily movable in the shaft. This makes it easy to move the container within the shaft. | A V bin is fixed onto the shaft. The only movement that you can execute is to rotate it within the shaft. |
Has a varying speed of blending. You can choose to operate the bin blender at either high or low speed. | V blenders are generally faster than bin blenders. However, the high speed comes with a high cost of production since it uses more electric energy |
Bin blender comes in handy for bulk production. It can easily blend large volumes of materials in different batches | It is very difficult to implement bulk processing with a V blender |
Bin blender is categorized under a free-fall type of blender. This simply means that the materials can fall freely from the blender to the bin. | The design of the V blender does not allow it to be grouped under the free-fall type |
Easy to discharge material from the IBC stainless steel bin blender | It is also easy to discharge material from the V blender. |
|
|
I hope that from the above differences you can easily decide on what you should buy, whether it is an IBC bin blender or a V blender.
Are there any disadvantages of bin blenders?
Throughout this guide, we have highlighted the numerous top benefits of buying and using IBC bin blenders. However, there is a high chance that you would like to know the drawbacks that come with using this bin blender.
Cleanliness of the bin blender
The first issue that you are likely to encounter is cleaning the big bin mixer. It is vital to note that the bins require regular cleaning, more so when you are planning to use them for blending different types of materials.
The good news is the simple design of the Senieer IBC bin blender makes them easy to clean, both inside and outside the bin. To make things better, the bin blender comes with an automated cleaning system. It does self-cleaning whenever you want. This means that you no longer have to worry about the cleaning problem of IBC tote bins blender.
Wear and tear problem
Since the IBC blending is characterized by mechanical forces, you may be worried about the issue of wear and tear of different parts. The wear can be due to the frictional forces on different parts of the bin blender.
The good news is IBC bin blender manufacturers have put in place adequate measures to address this problem. For example, the choice of stainless steel protects the body of the bin blender from effects of tear and corrosion.
Price of ibc bin blender problem
Like any other major equipment, you may be uncomfortable with the bin blender price. The cost of maintaining a bin blender may also be an itchy issue.
While this is a genuine issue, it will be better to compare the cost vs. the quality of the IBC bin blender that you are about to buy. The best bin blenders are likely to attract a higher cost than the inferior ones.
Also, you are likely to get the best deals when you buy directly from the best bin blender manufacturers and suppliers in China.
What is the working capacity of the bin blender?
IBC bin blenders come with different working capacities. You can buy either the smallest bin blender or the largest of them all. The capacity usually ranges between 500 liters to 3000 liters.
There is no best capacity, whether big or small. The best choice is the one that will match your production capacity.
What is the difference between bin blender and bin mixer
These two pieces of equipment seem to be synonymous as they almost serve the same purpose. But, what is the difference between them and which one should I buy?
The difference starts from the modes of operation. A bin mixer operates on the low shearing mixing with the ultimate goal of creating a homogenous solution. On the other hand, a bin blender is blending equipment that operates at a fast rate to create a homogenous solution.
There is also a major difference when it comes to the speed of production. Bin mixer operates in a slow mode. On the other hand, a bin blend mixes the material hence ideal for a fast-paced production room.
A bin blender can execute numerous operations under one piece of equipment. Apart from blending, it can also mix the materials. On the other hand, a mixer is designed for mixing purposes only, unless you modify it for other operations.
A bin mixer is quite aggressive when mixing the materials and products. It may end up creating noise. A bin blender operates gently to achieve the desired goal. This optimizes the quality of the blend.
What quality standards should a bin blender conform to?
One of the things that you should look at when buying bin blender in China is to verify whether it conforms to the industrial quality standards. These are standards that have been set by organizations and manufacturers are required to follow.
Here are some of the popular quality standards for the bin blenders;
Good Manufacturing Practices
cGMP is the most common quality standard that pharmaceutical equipment manufacturers are required to adhere to. cGMP provides guidelines for the quality of the products. Ensure that the bin blender meets this standard.
FDA standards
FDA is a regulatory body for food and drugs. It provides strict guidelines that should be followed by all players in this industry. It mainly highlights safety issues on the equipment to be used on food and drug processing. As we have seen, bin blenders are used for a wide range of applications and among them is in the food and pharmaceuticals. This automatically means that the blenders should be FDA-certified.
International Organization for Standardization (ISO)
The best organizations in the world are ISO-certified. This is proof the company is run professionally and is committed to meeting the needs of its clients. ISO also gives assurance about the safety of the products from the company.
European pharmacopeia standards
This is the standard for the bin blenders that are sold in the European nations. Manufactures should meet this standard before exporting their pharma equipment to the European region.
Does the bin blender that you are planning to buy meet any of the above standards? You should proceed to buy it confidently.
What is the difference between IBC bin blender, double bin blender, and multidirectional bin blender?
These three are among the most common types of bin blender pharmaceuticals. All of them are designed for the blending process only that they have different designs.
IBC bin bender comes in different shapes. Some are cylindrical while others have square and rectangular shapes.
What is the role of the rotating angle on a bin blender?
As we have seen, IBC bin blenders work on the principle of tumbling. A rotation angle must exist for the tumbling movement to be executed.
The rotating angle has an impact on the quality of the blend. A good rotating angle will ensure that there is a uniform and complete blending of the materials. Each particle of the material will be directly impacted by the movement of the bin blender.
So, even as you focus on increasing the rotating speed of the bin blender, keep your eye on the angle of the rotating axis.
How do you evaluate a new system?
There are various parameters that you can use for evaluating the performance of a new blender. One of them is speed. How fast can the bin blender execute the blending? This will have an impact on the quality of the blend. Another parameter is the power rating of the bin blender.
Can bin blenders deliver homogeneous blending?
Yes, it is possible to get a homogeneous material from a bin blending. You only need to use it as specified by the ibc bin blender manufacturer. It is also important to implement the requirements that will guarantee efficient blending.
Chapter 13: Conclusion
I hope that with this information, you will be in a perfect position to buy the best IBC bin blenders. The first step of getting the best bin blender is laying down your requirement specifications. Look at your manufacturing needs then decide on the specifications of the bin blender that will be a perfect match.
Once you have gathered your requirement specifications, contact the best bin blender manufacturer in China. We will have a deep discussion and see how we can meet your IBC bin blender needs. You can request modifications and customizations on the bin blenders.
If you are importing the bin blender, we will put measures to ensure that it is safely shipped to your country.